In Operation Environment Monitoring Site Risk Assessment动态环境监测点风险评估
动态测试时,由于受到众多因素的影响,均匀布点的原则已经不能真实反映房间内不同区域的环境状况。因此,需要采取风险评估的方法来选择动态环境监测布点,同时也为车间今后的日常监测布点起到指导意义。
环境监测是一种评估对生产环境控制的有效性工具。本风险评估的目的是应用ICH Q9(质量风险管理)的原则以及使用失效模式影响分析(FMEA)的风险管理工具,评估确定出空调系统PQ动态测试时的悬浮粒子及微生物布点位置。
1.Quality Risk Management Process质量风险管理流程
本风险评估使用ICHQ9推荐的质量风险管理流程图来确定空调系统最终的动态环境监测布点。但是本风险评估报告关于风险评估部分内容,如风险控制及质量风险管理程序的输出/结果、风险评审部分,在该文中只体现部分内容,并不详细介绍;风险评估的结果将作为空调系统PQ方案的一部分,从该风险评估报告到整个空调净化系统PQ结束,将一直贯穿着整个流程。
2.1Environment Monitoring Key Indicator环境监测关键指标
2.1.1Airborne Particle悬浮粒子
悬浮粒子(Airborne particle) 是悬浮在空气中、活或非活、固体或液体、粒径1nm~100μm的粒子。洁净区是一个对空气悬浮粒子浓度进行控制的区域,该区域的建造结构、装备及使用不仅能够截留粒子,而且会尽可能地减少粒子向该区域的介入,并且可根据需要对该区域的温度、湿度以及压差等参数进行控制。
Standard code of airborne particles in different clear area is as below:
洁净区各级别空气悬浮粒子的标准规定如下表:
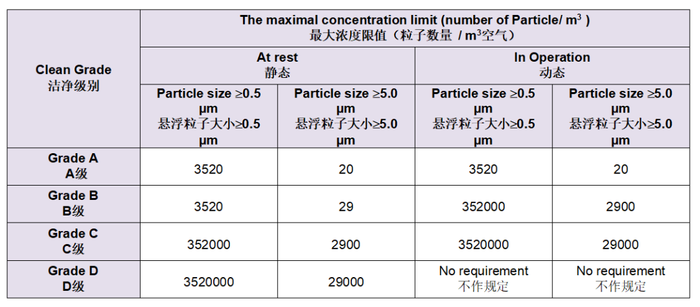
2.1.2.Microorganisms微生物
微生物分为以下三种类型:
浮游菌 (Airborne microbe) 是使用特定方法收集到的在空气中悬浮的活性微生物粒子,通过专门的培养基,在适宜的生产条件下繁殖到可见的菌落数。
沉降菌 (Settling microbe) 是使用特定方法收集到的由空气中沉降下来的活性微生物粒子,通过专门的培养基,在适宜的生产条件下繁殖到可见的菌落数。
表面微生物 (Surface microbe) 是使用特定方法收集到的吸附在洁净室(区)或设备表面的活性微生物粒子,通过专门的培养基,在适宜的生产条件下繁殖到可见的菌落数。
洁净区微生物监测的标准如下表:
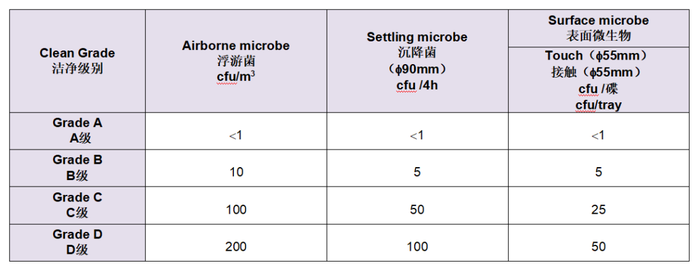
2.2 In Operation risk factors identification动态风险因素识别
当生产环境处于动态时,有很多风险因素可能影响环境污染甚至洁净环境破坏,每个风险因素都存在着不同的潜在的风险,所以,必须对每个风险因素充分的进行分析、评估,提出控制措施并进一步加以控制,以确保合格的动态生产环境。
动态是指生产设备按预定的工艺模式运行并有规定数量的操作人员在现场操作的状态。
“生产设备按预定的工艺模式运行”可理解为工艺设备在按照预定的工艺参数进行模拟生产或真实的生产活动。所以,在此过程中,除有特殊要求不得开启的设备外,其它洁净区内的所有生产及辅助设备应全部开启;
模拟生产活动时,设备在正常运转,但未投入生产物料和包装物,不存在真实的生产流程;
真实生产活动时,设备在正常运转,现场已投入生产物料和包装物,存在真实的生产流程。
“有规定数量的操作人员在现场”可理解为生产房间(区域)内存在的人数不超过房间最大容许人数,其中包括生产操作人员、环境监测人员、现场监督人员等;
“操作”可理解为操作人员在进行模拟生产操作或真实的生产操作活动;
综上所述,生产环境动态风险因素的识别应从人员操作、设备运转、物料特性、生产流程四个方面进行分析,我们用鱼骨图来表示所有的动态风险因素:
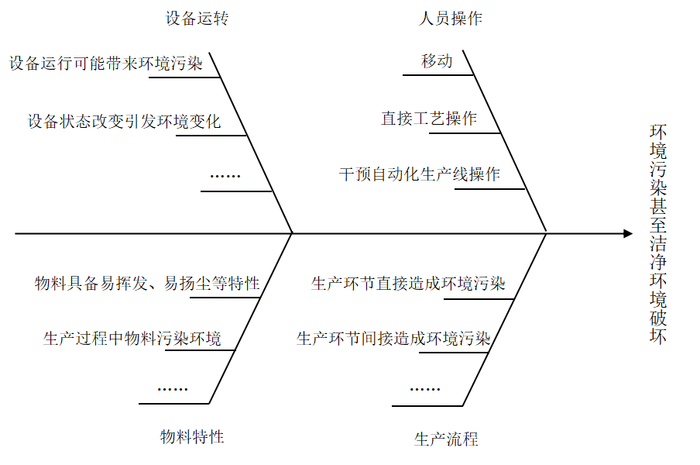
2.2.1 Personnel Operation人员操作
在洁净室的各项污染来源统计中,人是最大的污染源,人员导致的污染程度取决于他们所穿洁净服的防护级别,以及他们如何操作。
操作人员自身就是污染源,已操作人员在生产区内的移动轨迹可以标示出一条环境污染路线,
操作人员进入洁净区域内,站立或行走都有可能扰乱房间或单向流区域内的气流流型,进而影响相关区域空调系统的净化效果,从而造成环境污染;
在静态环境测试中,测试人员和监督人员不可避免的要进入洁净区并走动到各个区域进行测试,而在动态环境测试中,同样也存在此类的问题。所以,动态风险因素识别时,人员移动的关注度相对偏低。
·Direct processing operation直接工艺操作
人员在进行直接工艺操作时,不可避免的接触各类工器具和设备表面,从而带来环境污染;
人员在进行直接工艺操作的过程中,常带动各类工器具或改变物料状态(如,扬尘),从而带来环境污染;
人员在进行直接工艺操作的过程中,常改变设备的运行状态(整体或局部),可能间接带来环境污染。
·Interfere the operation of automatic production line干预自动化生产线操作
原则上,自动化生产线可以尽可能小的引入人员污染。但自动化生产线又常伴有人工干预,以解除异常状态,恢复正常状态。人员干预的过程中,因为人员自身污染问题,可能直接导致环境污染;人工干预的过程中,常改变设备的运行状态(整体或局部),可能间接带来环境污染。
2.2.2 Equipment running设备运转
设备运行过程中,常伴有摩擦、碰撞、震动等现象,可能形成各种碎屑(如轧盖机),从来带来环境污染。
设备运行过程中,可能伴有排热、排湿、排气等现象,可能改变环境中气流形态,间接影响环境质量。
设备运行过程中,活动部件的动作可能改变环境中气流形态,间接影响环境质量。
带有送风、排风的设备,运行和停止状态切换时,势必造成气流形态的变化,间接影响环境质量。
人员干预设备运行状态时,可能因局部部件的状态改变(如人工干预灌装机内安瓿瓶)影响气流形态的变化,间接影响环境质量。
2.2.3Characteristic of materials物料特性
-
-
-
药品生产过程中,很多液体物料可以随着环境的变化而产生挥发、凝结等现象,造成空气中悬浮微粒的存在,从而影响环境质量。
-
在对物料进行操作过程中,多种物料会随着操作发生状态变化(如,扬尘),从而影响环境质量。
2.2.4Production process生产流程
-
-
某些生产活动中直接产生污染物(如粉碎、称量、轧盖等),从而造成环境污染。
-
-
某些生产活动中伴随着产热、产湿等现象,可能改变环境中气流形态,间接影响环境质量。
2.3 In Operation sampling location risk Assessment动态取样点风险评估
2.3.1Risk Assessment methods introduction风险评估方法介绍
Phase 1, confirm the key room. Determine of key room will base on following risk factors:
第一阶段,确定关键房间。关键房间的判定将从是否具备以下几个风险因素考虑:
1.personnel operation人员操作
3.material characteristic物料特性
Phase 2, confirm the key location. Carry out risk factor analysis for each key room and ensure the location of risk factors, that is, the key location.
第二阶段,确定关键点位。对每个关键房间进行风险因素分析,确定风险因素的存在位置,即为关键点位。
Execution of risk Assessment is, to evaluate the severity and likelihood of potential hazard.
风险评估的执行,即,潜在危害的严重性和发生的可能性的评估。
Severity (S): when the hazard occurs, how far it will impact on the quality of products.
严重性(S):发生危害后对产品质量的影响程度
-
低(L):预期具有较小的负面影响。可预期所导致的危害具有非常微小到短期的有害影响。
-
中(M):预期具有中等的影响。可预期到其影响具有短期到中期的有害影响。
-
高(H):预期将具有非常显著的负面影响。可预期到其影响具有显著的长期影响和/或可能是灾难性的短期影响。
Possibility (P):Possibility of hazard upon production quality,
可能性(P):对产品质量产生危害的可能性
-
Low (L): Unlikely happen during products life cycle.
低(L):在产品的生命周期中不太可能发生。
-
Middle (M): Sometimes might happen during products life cycle.
中(M):在产品的生命周期中有时可能会发生。
-
High (H): certainly will happen some times during products life cycle.
高(H):在产品的生命周期中将会发生几次。
将把严重性和可能性合在一起来评价风险级别。将采用如下方法来确定风险级别:

评估的目的,是每个关键点位将根据风险因素而确定其风险级别。当风险级别为“1”时为风险可控,则不再给出建议措施。风险级别为“2”&“3”级必须给出合理建议,并决定适宜的控制方法。
给出建议措施之后应再次确认是否风险可控。
2.3.2 Confirmation of key room关键房间确定
当待分析房间存在上述所识别出的风险因素时,该房间可视作关键房间,分析过程如下表:
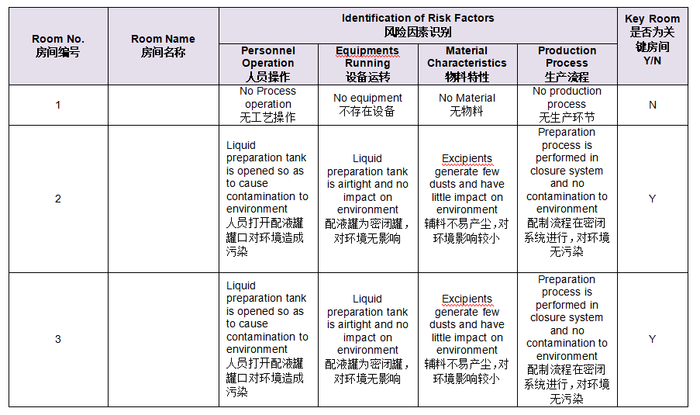
2.3.3 Confirmation of key location关键点位确定
在进行关键点位确定时,仅针对关键房间内的风险因素识别结果进行关键点位分析,详见下表:
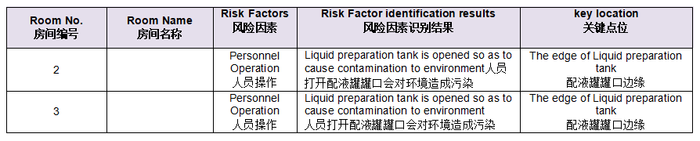
2.3.3.1 Key location risk analysis关键点位风险分析
在进行关键点位确定时,仅针对关键房间内的风险因素识别结果进行关键点位分析,详见下表:
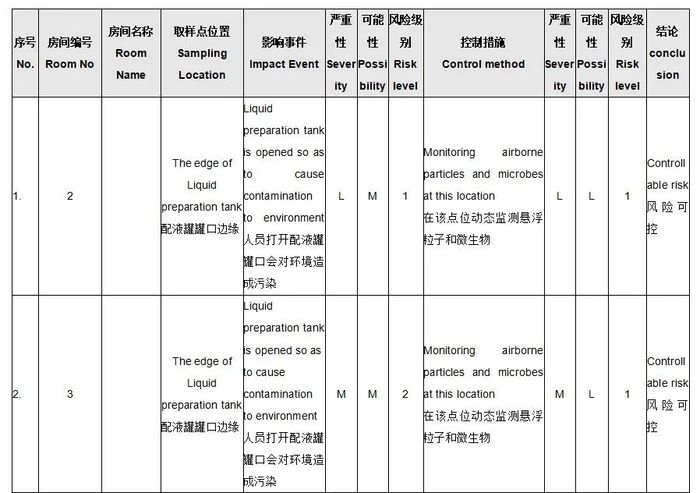
根据风险评估的结果在工艺设备平面布局图上绘制动态环境监控布点图,用于指导环境动态监测。
撰稿人 | GMP质量圈
责任编辑 | 胡静
审核人 | 何发
评论 0
正在获取数据......