制药行业的传统生产模式主要基于批次生产,即通过一系列离散的步骤完成药品的生产。这种模式虽然在历史上取得了巨大成功,但也存在一些局限性,如生产效率低、成本高、质量控制复杂等。连续制药作为一种新兴的生产模式,通过将多个生产步骤集成到一个连续的流程中,能够显著提高生产效率、降低成本,并确保产品质量的一致性。
连续制药技术的兴起主要受到以下几个因素的推动:
• 成本效益:连续制造能够提高设备利用率,减少生产周期,从而降低生产成本。
• 环境友好:连续制造减少了生产过程中的能源消耗和废弃物排放,符合可持续发展的要求。
• 质量一致性:通过实时监控关键质量属性(Critical Quality Attributes, CQA),连续制造能够确保产品质量的一致性。
• 法规要求:随着药品监管机构对质量控制的要求越来越高,连续制造技术能够更好地满足这些要求。
捷克Zentiva团队在不改变配方的情况下,成功将一种已获欧盟批准的高血压治疗药物从批次生产转为连续生产。该药物配方包含活性药物成分(API)、两种
微晶纤维素(Avicel PH-101和PH-102)、羟乙酸淀粉钠、二水合磷酸二氢钙以及
硬脂酸镁,其中辅料总占比为94.22%(w/w)。该团队系统优化了连续混合工艺的搅拌速率和停留时间等关键参数,并开发了基于
近红外光谱(NIR)的多变量数据分析模型,用于实时监测片剂成分和含量均匀度,替代传统质量控制方法。
通过NIR技术,该团队能够实时监控API的含量,确保整个连续生产过程的稳定性。在长达320分钟的不间断运行测试中,API含量始终保持在规定的质量标准范围内。这种实时监控与反馈控制机制不仅有效减少了质量问题的发生,还显著提高了产品质量的一致性。
根据产品需求预测、生产计划以及设备利用率的综合考量,该团队采用一条30 kg/h产能(每小时产128,000片)的连续直接压生产线(Continuous Direct Compression,CDC)。该生产线由三个主要串联单元操作组成:
1)IMA Cyclops MINI 预混合器结合了IMA 100L料仓,用于初步混合物料;
2)Gericke配方小车,包含三个独立的失重式喂料器,通过两个不同的入口将物料送入位于天平上的15升连续混合机;
3)Prexima 300压片机,配备了料位控制和NIR探头,以确保精确的填充和实时监控。
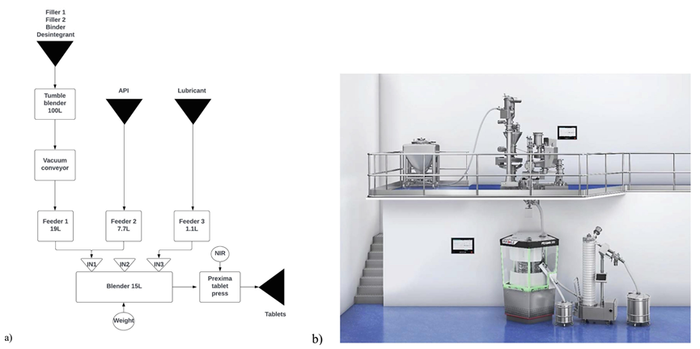
他们在上述生产线上,进行了320分钟的不间断运行测试,验证了多变量模型的有效性和工艺转移的可行性。结果显示,连续生产的片剂在崩解和溶出特性上与批次生产片剂相当,证明了连续生产工艺的可靠性和有效性。
连续制药面临的挑战
1. 技术复杂性
连续制造技术涉及多个复杂的技术环节,如实时监控、反馈控制、混合技术等。这些技术的集成和优化需要高度的专业知识和经验。
2. 法规合规性
连续制造技术需要满足严格的法规要求。药品监管机构对药品生产过程中的质量控制和法规合规性有严格要求,这增加了连续制造技术的实施难度。
3. 初始投资成本
连续制造技术的实施需要较高的初始投资成本。虽然连续制造能够显著降低生产成本,但初始投资成本较高,这可能会限制一些企业的采用。
未来展望
随着技术的不断进步和法规的逐步完善,连续制药技术有望在未来得到更广泛的应用。通过进一步优化实时监控和反馈控制技术,提高混合效果和产品质量一致性,连续制药技术将为制药行业的可持续发展提供重要支持。同时,通过降低初始投资成本,提高法规合规性,连续制药技术将为更多企业提供可行的解决方案,推动整个行业的技术进步。
参考资料:
Waněk, A. et al. Manufacturing process transfer to a 30 kg/h continuous direct compression line with real-time composition monitoring. International Journal of Pharmaceutics 656, 124100 (2024).
评论 0
正在获取数据......