原料药的析晶/精制工艺会影响产品的杂质谱、晶型及粒度等,需注意说明粗品的纯化/精制方法,在工艺开发及小试研究部分确定纯化/精制工序的相关工艺参数,并通过工艺验证对最终的工艺进行确认,确保工艺的稳健性。
本文对影响原料药纯化/精制的关键工艺进行分析,以期对同行有所启示。
以X原料药为例,对其析晶/精制过程中需要考虑的问题进行详细论述,具体如下:
如X原料药,在不同的有机溶剂中与氢氧化钠溶液反应生成钠盐,同时引入结晶水,控制其水分含量在合适的范围内,在此过程中从产品的收率、产品的水分含量、析晶的方式等三个方面评估工艺的优劣。可能的试验结果如下:乙醇作为溶剂产品无法正常析出,甲醇作溶剂产品的水分含量不合格,乙腈作为溶剂析出速度很快但是结块严重,离心过滤困难,四氢呋喃则收率偏低。异丙醇作为溶剂的效果从收率、水分含量、物料性质等方面对比明显优于其他几种溶剂。
综合考虑析晶效果、水分含量、收率方面的结果,确定采用异丙醇作为溶剂,氢氧化钠水溶液缓慢加入的方式进行成盐析晶。
该原料药在异丙醇中析晶较慢,在加入晶种诱导析晶后,整个析晶的速度加快,但是在析晶不完全的情况下仍然会导致收率偏低,因此在优化工艺过程中重点考察了不同析晶时间对收率与纯度的影响,结果如下:

实验结果显示,当析晶时间达到18小时后,产品的收率变化较小,延长时间对产品的收率与纯度几乎没有影响,考虑到放大生产过程中搅拌方式等变化,将最终的析晶时间确定为18~24小时。
由于该原料药析晶速度较慢,尝试加入目标晶型的原料药作为晶种进行诱导析晶,并对晶种加入量进行筛选,实验结果如下:
晶种加入量的考察结果汇总
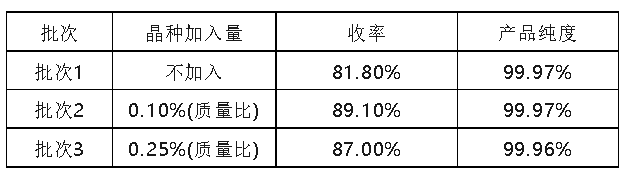
研究结果表明:在不加入晶种的情况下,产品析出速度慢,析晶时间长,而在加入晶种后固体析出的速度明显加快,并且诱导析晶的方法使产品晶型及质量的控制过程更稳定。晶种用量的增加对析晶过程与产品质量影响不明显,因此最终确定析晶过程中晶种的用量为0.1%(质量比)。
在不同的温度下析晶可能会影响产品的收率与纯度,在加入晶种后考察了不同析晶温度下产品的收率与纯度,实验结果如下表所示:
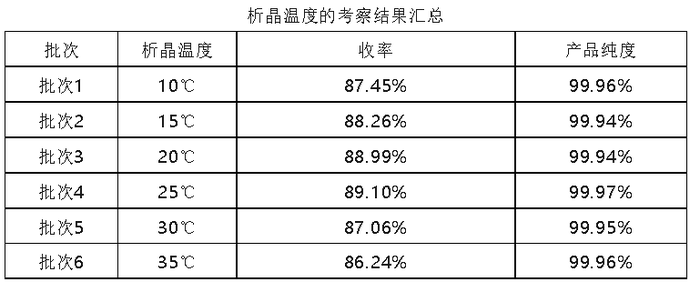
试验结果显示:不同温度下该原料药在确定的有机溶剂中析晶后,批间的收率与纯度没有特别明显的差异,但实验过程中可以明显的观察到温度较低的情况下该原料药不易溶解,在原料无法完全溶解的情况下目标产品已经从溶液中析出,从而造成了固体物料相互包裹的实验现象;而温度较高则出现了析晶太快,放大批量制备后过滤时间不足的情况。综合以上考虑,最终选择的析晶温度为20~25℃。
不同的干燥温度下,产品有高温降解的风险,为了确定干燥过程中高温对产品的影响,选择了不同温度下考察产品的稳定性,进而确定最终干燥的温度,实验结果如下标所示:
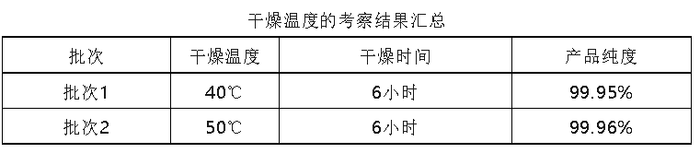
试验结果显示:产品在40~50℃干燥过程中产品质量没有明显变化,产品在丙酮打浆后干燥,由于丙酮沸点较低易挥发,最终选择40~50℃的范围内对成品进行干燥。
为兼顾成本和环保,原料药合成过程中溶剂回收在所难免,但是溶剂回收过程必须受到控制和监测,并应符合适当的内控标准,回收次数应进行验证。结晶(纯化)溶剂的回收按照所处反应步骤的不同,也会有不同的杂质含量。一般来说,作为终产品的重结晶(纯化)溶剂所含杂质种类较为明确,且含量可控,此类溶剂回收的控制相对容易。
对于诸如甲苯或丙酮等含有苯的溶剂,苯残留也应纳入检测项目。此类溶剂随着回收次数的增加,其中苯的累积量可能伴随增长。因此,制定合理的内控标准对于控制成品中苯残留以及确定溶剂回收次数都是十分必要的。
很多原料药合成工艺中可能存在返工操作,但返工工艺需进行详细研究。对于返工的产品,可能需要进行额外相关项目的检验及稳定性考察。需对以往的返工批次进行汇总分析,调查返工原因,并对返工操作进行验证,以确保原料药的质量不会受到过度反应物和其它副产物的不利影响。
原料药的析晶/精制工艺对产品质量影响显著,需在工艺开发过程中就对其进行考察和研究,确定合适的析晶/精制工艺,以稳定保证产品质量。
参考文献
1、药品GMP指南:原料药【M】
2、化学合成原料药生产工艺中溶剂回收的GMP相关要求.王宏亮
3、溶剂手册(第五版)
撰稿人 | ZWX 药事纵横
责任编辑 | 胡静
审核人 | 何发
评论 0
正在获取数据......