文/王兵 李伟敏 邹小安 方明全 欧阳健均就职于无锡药明合联生物技术有限公司。
振动检测
随着数据信息量的大幅度提升以及5G技术的发展,基于5G的边缘计算技术已成为一种实时高效的数据处理方式且被广泛使用。机械设备的故障中有相当一部分是由滚动轴承失效引起的,所以如果能通过实时监控滚动轴承的运行状态,在滚动轴承失效之前就进行更换,将能大幅度降低此类事故的发生。现在,随着5G边缘计算技术的进步,这样的设想已经成为了现实。
采用加速度传感器来检测轴承振动的加速度,结合滚动轴承的时域和频谱特征,通过傅里叶变换[1]、神经网络算法和聚类算法[2]对轴承分类状态进行识别,可实现对滚动轴承的实时状态监测,如图1所示。
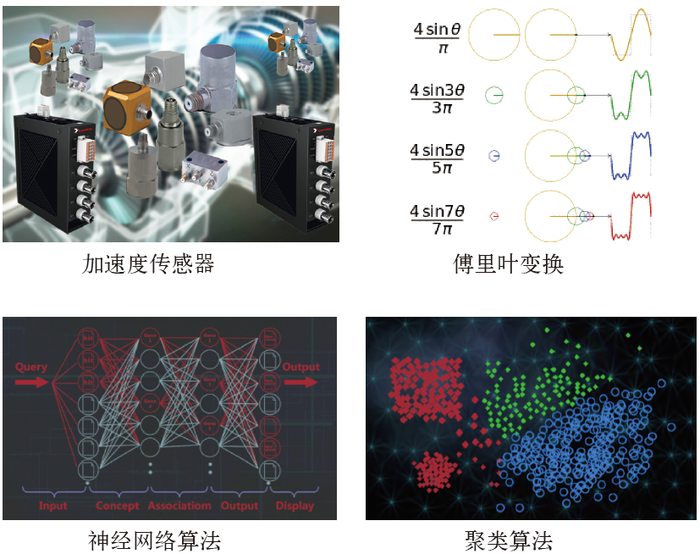
图1 通过4 种设备及技术可以实现滚动轴承的实时监控
振动检测的数据再通过5G边缘计算,便能区分出是动平衡、对中的问题,还是轴承出现了损伤,且给出一个各项缺陷占比的报告。
将振动检测用于轴承的视情维修
理论上,由电机带动的滚动轴承能被观测到的物理参数至少有如下几个:电机运行的电流、轴承运行的振动、轴承运行的杂音以及轴承部位的升温(它们不一定都能用来进行预警监测)。
对于旋转机器的振动监测和分析,主要是评价其运行的健康状态,发现和诊断可能存在的潜在故障,包括:不平衡、轴弯曲、偏心、不对中、共振问题、基础松动、轴承问题等。轴承的问题又可以进一步分为:磨损失效、疲劳失效、腐蚀失效、压痕失效及胶合失效。
按照以可靠性为中心的维护(Reliability Centered Maintenance)[3]理论,在技术可行和实行有价值的情况下,主动性维修中应首选视情维修,且应以小于P到F的时间间隔期进行视情维修,如图2的运行状态图所示。从图2中可以看到失效迹象最敏感的是振动,依次是杂音、升温和发烟,而电机的电流不能够作为判断的依据。敏感程度排序依次为:振动→杂音→升温→发烟。
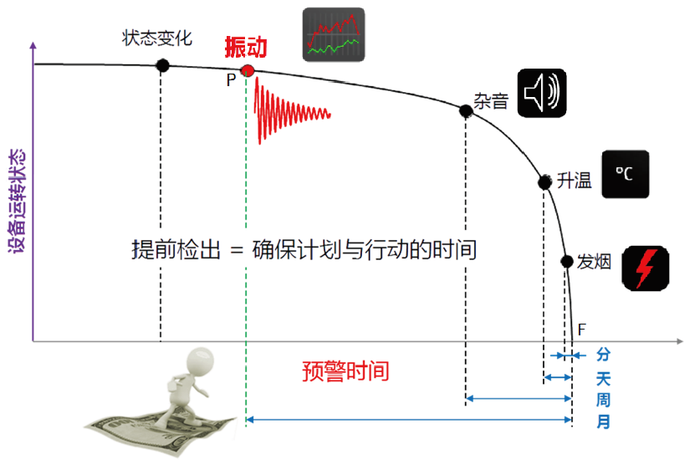
图2 设备运行状态示意图
从出现振动到失效会有数月的周期间隔,从出现杂音到失效也会有数周的周期间隔,从出现升温到失效只有几天的周期间隔,从出现发烟到失效就仅有几分钟的时间。图2中P点为潜在失效点(Potential Failure),F点为失效点(Failure)。在P点之后,随着失效迹象的进一步明显,依次会出现杂音、升温,等到出现发烟,设备很快就会失效了。在P点之前发生的故障,则纯粹是概率事件,所以无法预测。
轴承的振动检测理论上仅需要定期进行,实施的检查周期只要短于P到F的时间间隔,即如果采用振动监测来进行视情维修,其检查的周期只需要小于1个月。然而在发现轴承潜在失效后,尚需要进行处置和恢复的时间,这个处置和恢复必须在失效前执行完毕。为此,包括行动时间在内的整个检查周期都应小于P到F的时间间隔,考虑到振动检测的成本不高且方便,建议设置为2~3周。当然,如果能做到实时监测,就可以更好地维护设备,并进行如图3所示的平台化管理。
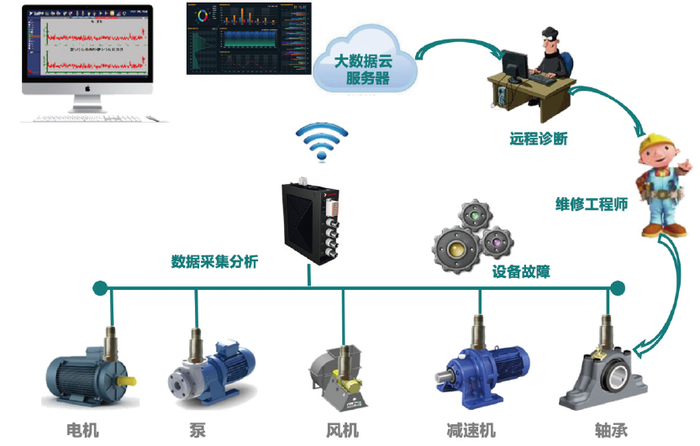
图3 振动监测的架构示意图
有些制药公司本来就建有SCADA系统(数据采集与监视控制系统),其服务器可以设置在云端或本地,监测结果可以实时从手机的APP上获得。由此看来,用振动监测来进行旋转设备的视情维修,是一个运用以可靠性为中心维护理论的教科书般的案例。
【参考文献】
[1]曹瑞华.傅立叶变换及其应用[J].理论数学,2014(4):138-143.
[2] 浙江远盟自动化技术有限公司.大数据故障诊断系统[Z].2021.
[3] John Moubray.以可靠性为中心的维修[M].北京:机械工业出版社,1995.
评论 0
正在获取数据......