自2017年以来,Hügli公司前后斥资超过3000万欧元,在德国南部新建生产基地,扩大生产汤料、酱汁、高汤、调味品、甜点及速食产品等各类干混制品。该工厂因面对小批量、多组分(多达1000种各类原料)的海量订单,要求设备供应商必须提供柔性的自动化原料输送和混料与计量系统,确保无交叉污染并完成高品质的生产,年产能达4万吨,每小时产出12批次成品混合料,每批容量2000升。
为满足Hügli公司的上述要求,如果所有原料(大中小料)的移动都采用传统的气力输送和计量系统,为了避免众多中料和小料的交叉污染就必须采用多管系统和相应的配合部件,同时因一些原料极易吸湿结块,造成堵管,对于维持正常生产将是极大的挑战,另外,更高的系统设备投资和未来的设备维护费用也是必须考虑的。而移动式料罐配料系统恰好能够完美的解决上述中料和小料的输送和配料问题,Hügli公司最终经比较决定选择奥地利Daxner公司提供整体解决方案。
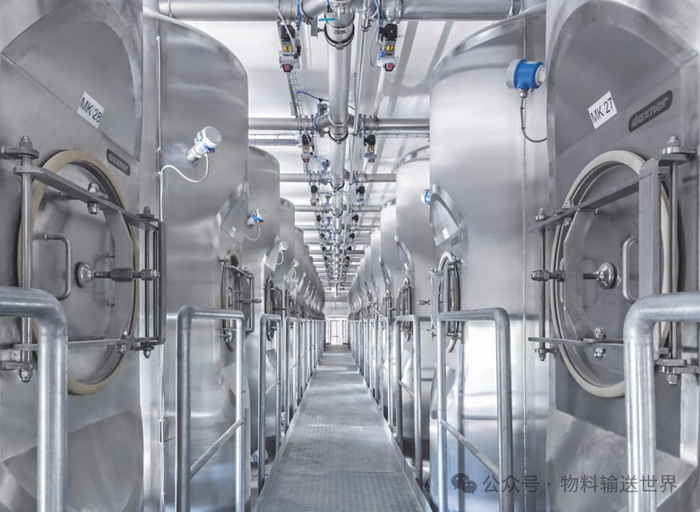
Daxner的整套移动式料罐配料系统配备DCS与自动导航车(AGV)系统,DCHD系列料罐全部采用卫生级设计,容量1200升,支持CIP清洗。
创新的工艺技术
Daxner的整套移动式料罐配料系统横跨3层结构,覆盖4000平方米生产区域,完整集成从户外筒仓原料存储、日仓输送、填充计量、称重到6条独立混料线加工,直至IBC出料的全程自动化流程。Daxner开发的创新型系统整合易清洁设备设计、无尘粉末处理及防交叉污染技术,可全方位保障产品完整性。
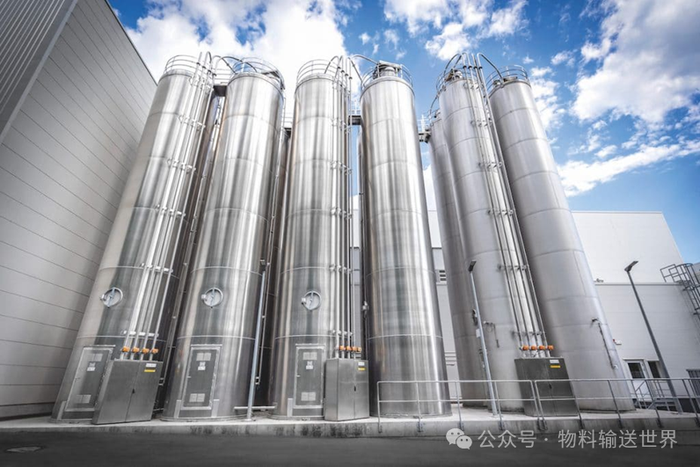
所有原料按组分规模分为大、中、小三类:
- 大宗原料:存储于10座户外筒仓,通过气动输送至4条混料线;
- 中型原料:由30个日仓储存,通过袋装投料站与吨袋卸料系统供料;
精密称重:40个称重站依据原料特性分配至不锈钢日仓下方,中型原料计量称重全程自动化,精度达±50克。
千余种小料存储于配备9000个料箱的自动化立体库中,所有单次用量低于1公斤的配方均在此进行人工管理与计量。订单管理系统自动调取所需原料,输送至4个手动计量站。操作人员按条码标识将各组分装入转运槽后,料槽返回立体库暂存。
柔性洁净的DCS料罐移动系统
50个容量1200升的IBC通过4台AGV在出料区全厂流转,精准定位至目标工位。空料罐由输送系统自动抓取并定位至对应称重站下方。采用激光导航将IBC精确移动至对接点,经Daxner料罐对接站DCDS提升后完成原料填充。
预称重技术使IBC填充速率高达12个/小时。完成自动计量后,IBC被运送至4个手动加料站之一,人工添加小料后由AGV系统转运至混料线上方升降平台,经电动叉车定位至Daxner料罐出料站。该站配备自定心框架与对接接口,可搭载振动电机实现无残留卸料。
4台强力犁刀式混合机确保物料快速均匀混合,成品经吨袋包装后输送至包装工段。
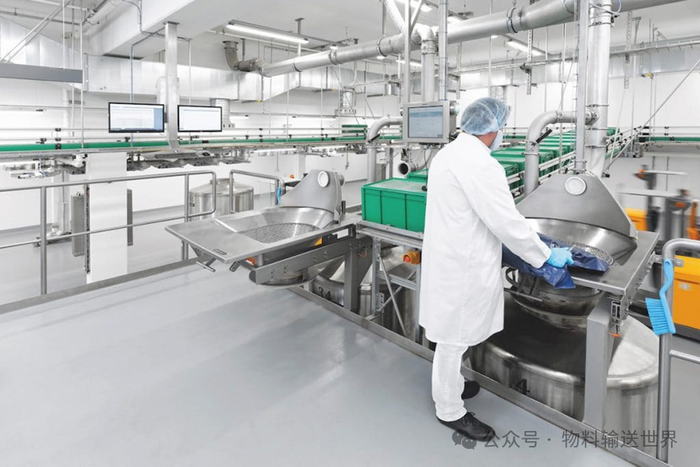
每套Daxner的生产系统均为客户专属定制。卓越的工程设计结合自主生产能力,将细节技术方案转化为完整的工厂概念:
- 料罐出料系统:集成自动阀控装置,通过双气动缸实现阀门全自动启闭。紧急情况或清洁时可通过手动杠杆操作。料罐出料配备自动翻板启闭器;移动式袋装投料站
- 移动式吨袋卸料站:日仓由先进移动式吨袋卸料站填充。装载平台位于日仓上层,通过嵌入式填充喷嘴连接。卸料站通过杠杆机构形成封闭无尘系统。
- 多尺寸吨袋对接系统:传统系统仅适配单一吨袋规格。Daxner创新设计可轻松调节对接站以适应不同尺寸,简化吨袋操作流程。
(图片:Daxner)
精准计量确保每次完美配比
中型原料存储于日仓,通过移动式吨袋卸料站供料
智能控制系统
工厂控制系统实现工艺与控制的完美协同。ESAweight系统对接企业ERP,全程监控、记录并协调容器运输与自动计量流程,其核心优势在于操作便捷性、全程可追溯性及并行订单处理能力。 。
Hügli德国公司于2017年按国际食品标准(IFS)投入运营以来,一直以高质量与卫生理念确保最高的生产工艺安全性。
评论 0
正在获取数据......