发酵系统设计在生物制药领域扮演着至关重要的角色,它直接影响到生产效率、产品质量以及运营成本。本文旨在探讨发酵系统设计的核心要素,从系统构成到各关键组件的设计考量,以期为该领域的工程师和技术人员提供实用的参考和指导。通过深入分析发酵系统的各个部分,揭示如何优化这些设计要素以提高整体系统的性能和可靠性。同时,结合珐成浩鑫在发酵领域的实际案例,本文将展示先进设计理念在实际应用中的成功实践,为发酵系统设计提供宝贵的经验和启示。
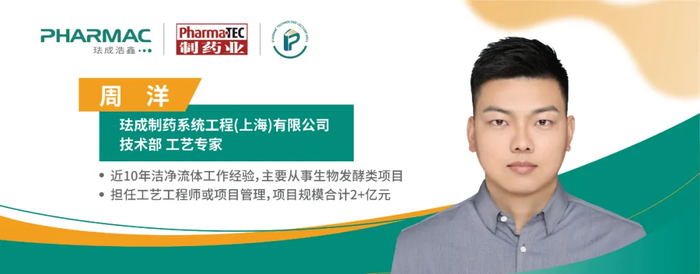
“发酵”(fermentation)一词源自拉丁文“fervere”,意指“发泡,翻腾”,最初用来描述果汁或麦芽浸出液中的糖在酵母菌无氧呼吸作用下降解,产生二氧化碳(CO2)的现象。[1]
现今,发酵一词通常指“在合适的条件下,利用生物细胞内特定的代谢途径转变外界产物,生成人类所需的目标代谢产物或菌体的过程”,也就是所谓的“工业发酵”。
发酵工程有时也称为“微生物工程”,是生物工程(涵盖基因工程、细胞工程、发酵工程、酶工程和蛋白质工程等)中的关键技术之一。
下表展示了发酵的历史,以及人类对微生物认识的演进过程:
表 发酵历史与关键节点[2]
时间 |
事迹 |
时期 |
公元前3500年 |
人们开始用人畜粪便和秸秆进行堆肥 |
自然发酵时期 |
公元前3000年 |
人们开始用麦芽制作饴糖,使用散曲来制酱、酿醋,制作泡菜,以及发酵奶酒,制作干酪和豆腐 |
公元前2000年 |
古希腊和古罗马人已经掌握了用葡萄来酿造葡萄酒的技术 |
1675年 |
荷兰科学家列文虎克发明了显微镜,并首次观察到了微生物的存在 |
纯培养技术建立 |
1857年 |
法国科学家巴斯德证明了发酵过程是由微生物引起的,并发明了巴氏杀菌法 |
1897年 |
德国科学家比希纳证明了发酵过程是由酶所驱动的 |
1905年 |
德国柯赫应用固体培养基分离培养物 |
1929年 |
亚历山大·弗莱明发现了青霉素 |
深层通气搅拌 |
1938年 |
英国的弗洛里和钱恩实现了青霉素的量产 |
1950年 |
日本木下祝郎成功实现谷氨酸发酵 |
代谢调控 |
1952年 |
微生物甾体类药物转化取得成功 |
1960年 |
石油微生物的研究与应用,微生物消除环境污染 |
原料转变 |
1970年至今 |
分子生物学的发展,细胞融合技术,基因扩增方法,以及重组DNA技术的发展 |
基因工程 |
为了达到大规模工业发酵的目标,需要采用多样化的发酵方式和过程。这些过程通常按发酵工艺的特定方面进行人为划分,例如按菌种类别、呼吸类型、培养基类型、补料方式、发酵规模等。
无论采用哪种分类方法,发酵过程大致包括以下几个阶段:菌种活化、培养基的配置、培养基和发酵罐等设备的灭菌、菌种的扩培、发酵过程的工艺放大、发酵下游产物的分离、产物的包装以及废液的处理等。
关键技术环节主要包括:菌种选育、纯培养、发酵过程优化、发酵过程放大以及发酵工程下游分离纯化等。本文所指的发酵或发酵系统,主要涉及纯种培养及其放大过程。[1]
通常,一个发酵系统由以下核心部分构成:罐体及其附件、控温系统、进气过滤系统、尾气调节系统、补料系统、取样及放罐系统、以及CIP/SIP系统等。
本文所讨论的发酵罐特指容积大于5L的不锈钢夹套发酵罐,而容积小于5L的发酵设备一般采用单层玻璃罐。
发酵罐的结构设计与发酵类型密切相关。例如,好氧类发酵罐需设计成瘦高型,其高径比通常在2.5~3之间,以确保氧气能够充分溶解。
根据发酵类型的不同,搅拌系统的设计也有所差异。常见的搅拌桨叶形式包括:涡轮推进桨、四宽叶桨、抛物线桨、六直叶桨、六斜叶桨、消泡桨等。
发酵罐是一种通用性较高的设备。例如,标准发酵罐采用蝶形上封头或平盖上封头与蝶形下封头的组合。对于容积低于500L的发酵罐,可采用筒体法兰配合上盖提升的设计;采用顶部中心机械搅拌,在发酵容积较小或料液粘度较低时,也可采用磁力搅拌;罐体通常配备夹套和保温层,以便在发酵过程中及时调控罐内培养温度;考虑发酵时间较长,建议配置双机械密封及无菌冷却水系统,以确保发酵过程的洁净度。为方便在培养过程中进行检测,通常会配置双口无菌取样阀,以实现独立的灭菌、清洗和取样操作。
发酵系统是一套高度自动化的系统,配备了过程检测仪表,包括温度变送器、压力变送器、泡沫液位计、pH传感器、DO传感器等,甚至一些发酵罐还配备了浊度仪,更加高端的发酵系统甚至配置了拉曼光谱仪。
为了确保菌种的健康生长,适宜的温度是必须的。同时,为了避免杂菌生长,必须对发酵罐和培养基进行灭菌处理。因此,不锈钢发酵罐通常设计为三层夹套罐,通过向夹套内通入蒸汽或冷冻水来实现对罐内温度的控制。
发酵罐夹套也可采用内置循环水路的设计,通过对循环水进行升温和降温的操作,实现对发酵罐内温度的调控。这种串级控温的优势在于,它避免了因公用工程媒介变化而导致的罐内温度剧烈波动。同时,循环水采用比冷冻水更清洁的软化水或纯化水,以提高夹套内的洁净度,从而减少铁锈的生成。
发酵系统的通气操作具有双重目的:首先,系统灭菌后通过通气来保持系统内的正压;其次,好氧型发酵过程需要大量的空气或氧气以支持菌体的生长。因此,在灭菌后或培养过程中进行通气操作时,必须确保通入系统的空气是无菌的。在设计上,空气或氧气通过0.22μm 的PTFE滤芯进行除菌过滤。
气体过滤器可采用单级或双级过滤设计,且过滤器支持单独清洗和灭菌操作。气体管路的调节则采用质量流量控制器(MFC)进行精确控制,后端配备浮子流量计以实现就地显示。在靠近罐体时,应设置反流装置等安全措施。
如前所述,发酵系统在灭菌后需要通过通气进行保压操作,保压时的压力调节是通过尾气管路中的调节阀来控制的。
同时,尾气系统还设置了尾气冷凝器,尾气加热器和尾气过滤器等设备。发酵罐在培养过程中会不断地向外排放尾气。为了避免尾气夹带液滴,尾气首先会通过冷凝器进行液化处理,然后通过加热器进行干燥,最后通过过滤器去除细菌和异味。过滤器有时采用并联双过滤器设计,一只工作,一只备用。当其中一只过滤器发生堵塞时,系统会自动切换到另一只。每个过滤器都可以单独进行灭菌处理,以便在生产过程中更换并重新投入使用。
细胞的生长和菌种的繁殖需要依赖于一定的物质基础。根据不同的培养对象,企业需采用不同的补料策略。有些培养过程可以在接种前一次性将所需的培养基全部转入发酵罐内,而有些则需在不同的生长阶段逐步添加所需的营养物质。
对于简单的一次性补料,可以采用插针法。而对于复杂的补料过程,则需采用密闭管路,并通过蠕动泵进行连续流加。
在补料前,手阀和蠕动泵软管必须先经过灭菌柜进行灭菌处理,然后在洁净台内完成组合,并将组合后的设备移至生产车间进行管路连接。之后,对补料管路进行单独灭菌,确保其安全使用。
对于热敏性物料,由于不能承受高温灭菌,因此采用在线除菌过滤的方式。过滤器可以单独进行灭菌,同时在过滤前后配置压差监测,以监测滤芯是否出现堵塞。
为了实现对培养过程中相关指标的有效监测,发酵罐配置了pH电极,DO溶氧电极、温度电极等传感器。同时,某些参数,例如细胞产物,需通过取样操作进行离线检测。无菌取样阀一般设置在罐体的侧壁,靠近最低发酵量的位置,确保取样前后可单独进行清洗和灭菌。同补料操作相同,取样用的瓶子和手阀也需要先经过灭菌柜灭菌,然后才能接入系统。
由于发酵系统对无菌性要求高,因此通常采用一体焊接的罐底阀或带有支阀的罐底阀。放罐操作比较简单,只需选择不同的放罐对象,由系统进行压料即可。
清洗和灭菌是保障发酵系统无菌性的重要手段,它们是培养成功的基础。因此,发酵系统的CIP和SIP通常是验证的重点对象。
发酵系统的清洗管路和灭菌管路高度重合,几乎在所有需要清洗的地方也必须进行灭菌。因此,在系统设计时,通常会考虑将这些管路合并,以简化操作。
系统的清洗可以分为罐体清洗和管路清洗两个部分。管路清洗时,可按功能或管径进行分组,例如,补料管路可同时清洗多路。在设计时,需要考虑清洗主管的流量和流速,以确保合并的管路数量不会太多,从而保证清洗效果。但是减少合并的管路数量会增加总的清洗时间,这也是设计者需要特别关注的问题。
珐成浩鑫在洁净管道领域拥有三十多年的丰富经验,为生物制药、日用化工、合成生物及相关行业提供专业的洁净流体系统工程服务。作为一家专注于打造模块工厂、智能工厂、合规工厂总体解决方案的专业化公司,珐成浩鑫致力于推动流体工艺技术的创新突破,并打造具有自主知识产权的工艺装备,实现高质量、可持续的洁净流体设备本士化制造之路。
公司重点发展以工艺工程服务为核心,包含发酵系统、配液系统、水系统和自控的智能化MES及工艺自动化。珐成浩鑫致力于整合MES和ERP,为企业提供全生命周期的GxP咨询及验证服务,从而为企业量身定制符合实际需求及未来发展的完整解决方案,部分案例现场图片如图1、图2、图3所示。
图1 杭州某生物发酵项目(含30L-60L-150L-500L-1000L发酵系统三套)
图2 苏州某生物发酵项目(含50L-700L发酵系统一套及下游纯化线)
图3 苏州某生物发酵项目(含50L发酵系统一套及CIP系统)
目前,公司已经形成了以“P-G-I”为核心的专业洁净流体系统服务:
● Process:洁净流体工艺系统模块化设计,制作安装及调试(适用于制药、高端精细化工、食品饮料等行业);
● GMP:GMP验证咨询服务;
● Intelligence:信息化系统(C&IS/MES/SAP Business By Design)的设计与实施;
珐成浩鑫的愿景是通过持续创新和专业服务,为客户创造核心价值,成为最佳合作伙伴。珐成浩鑫将继续秉承“尊重,诚信,开放,共赢”的理念为客户提供高质量洁净容器、生物反应釜、洁净工艺管道等模块化系统,自动控制及信息化系统,以及GMP验证等服务。
参考文献:
[1] 高大响. 发酵工艺[M].北京: 中国轻工业出版社, 2019.
[2] 于文国,张铎.发酵生产技术(第4版)[M].北京:化学工业出版社, 2020.
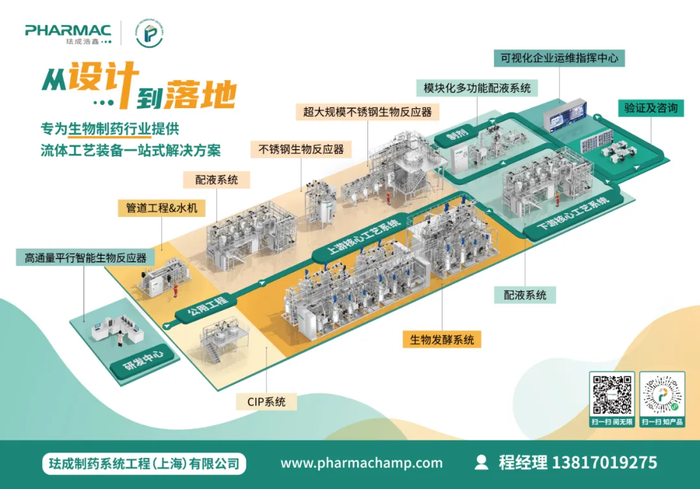
点击查看珐成浩鑫XBioR不锈钢生物反应器解决方案
评论 0
正在获取数据......