无菌制剂生产是生物医药领域的关键环节,其核心挑战在于如何在复杂的工艺流程中有效防控污染与交叉污染,确保产品质量与患者安全。抗体药物偶联物(ADC)等高风险制剂的生产对设备设计、环境控制及操作规范提出了更为严格的要求。本文以东曜药业 ADC 制剂生产实践为基础,系统探讨了洗瓶机、隧道烘箱、灌装机、隔离器、冻干机、轧盖机及外洗机等关键设备在设计与运行中的交叉污染控制策略(Cross-Contamination Control Strategy, CCS)。通过分析设备设计、运行中的相关管理措施及创新实践,为行业提供了一套可借鉴的无菌生产解决方案。
无菌制剂生产过程中涉及高活性成分(如细胞毒性药物、ADC 等),其交叉污染风险不仅影响药品质量,还可能严重威胁患者生命安全。根据 FDA 的统计数据显示,全球约 15% 的药品召回事件与无菌生产中的污染相关。特别是抗体药物偶联物(ADC),由于其复杂的双组分结构(抗体与毒性小分子的结合),在交叉污染控制方面面临双重挑战:既要防止高活性细胞毒性成分的外泄,又要避免药物本身的生物污染。
东曜药业作为中国领先的生物药CDMO 企业,其 ADC 生产平台覆盖了从研发到商业化的全流程,并配备了OEB5 级高密闭生产线及年产能 530 万瓶的规模。通过对东曜药业设备设计与运行策略的深入研究,本文可为行业提供以下价值:
● 系统性地总结高风险制剂生产中的 CCS 实施路径;
● 提炼隔离器技术和在线监测等核心技术的优化方向;
● 推动 GMP 规范与智能化技术的深度融合。
交叉污染是指在生产和储存过程中,不同产品或物料因物理接触或环境传播而导致的非预期混合。其主要来源包括:
● 设备残留:生产设备未彻底清洁导致的批次间污染;
● 人员操作:操作不规范引入的微粒或微生物;
● 物料本身:物料中存在的微生物或颗粒污染;
● 环境因素:HVAC 系统失效、压差失控等;
● 方法流程:操作方法或清洁方法存在缺陷,难以有效去除残留。
根据 ICH Q9 及 PDA TR54 指南,CCS 需基于质量风险管理(QRM),并涵盖以下关键维度:
● 预防性设计
:通过提高设备密闭性和采用冗余过滤系统降低污染概率;
● 过程控制
:实时监测关键参数(如粒子数、浮游菌、压差);
● 清洁验证
:采用 TOC(总有机碳)分析和微生物限度测试确认清洁效果;
● 应急响应
:制定并实施污染事件的标准化处理流程。
3.1 洗瓶机与隧道烘箱:清洁和无菌的保障(参见图1)
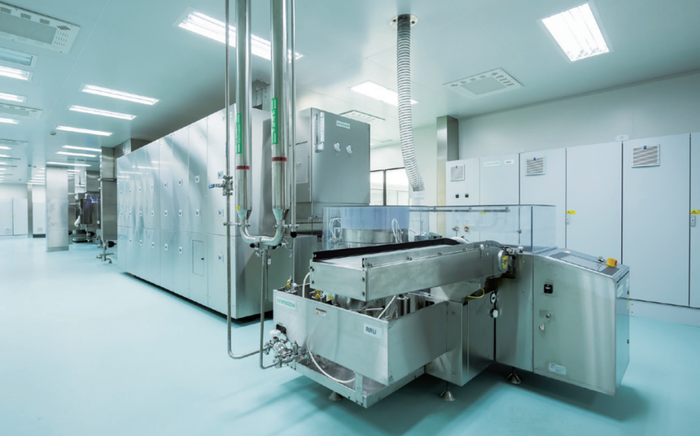
图1 洗瓶机及隧道烘箱
● 水气过滤系统
:采用两级过滤(预过滤 +0.22 μm 除菌滤芯),确保清洗水与压缩空气中的微生物与微粒得到有效控制。针对 ADC 的高活性特性,尾端水汽需通过 BIBO 高效过滤器处理,防止毒性物质扩散;
● 超声波清洗技术
:通过空化效应清除瓶内壁微粒,功率需定期校准(±5% 误差限),避免因能量衰减导致清洗不彻底;
● 除湿罩设计
:抽掉洗瓶产生的湿气,抽湿风机要避免倒灌;
◆ 分段压差设计:预热段(+10 Pa)、灭菌段(+15 Pa)、冷却段(+12 Pa),平衡热原去除与背景环境稳定性;
◆ 风速调控:监控隧道烘箱风速,确保除热原效果,同时兼顾层流保护与能耗效率;
◆ 在线粒子监测:在冷却段安装激光粒子计数器,实时反馈动态洁净度;
◆ 冷却段灭菌:冷却段要配备在线灭菌功能,每批生产前需进行冷却段灭菌。
● 清洁
:水箱每次使用前执行清洗和吹扫,每次生产结束后清洗并用压缩空气吹扫排空;
● 水、气压力
:经清洗效果确认的水、气压力,按照设备确认的最低限设置为报警限;
● 碎瓶应急
:破瓶时立即启动“碎瓶模式”,隔离影响区域的瓶子,并做废弃处理;
● 周期性验证
:每年进行热分布(Mapping)等测试,确保隧道烘箱除热原效果。

图2 灌装机
● 冗余除菌过滤
:在必要时采用“双滤器并联”设计,单个滤器的截留效率需≥ 99.99%(LRV ≥ 4),滤器安装位置需靠近灌装针(距离< 1 m),减少管路污染风险;
● 蠕动泵精准控制
:通过伺服电动机驱动,实现灌装精度达 ±1%,同时避免离心泵的剪切力对 ADC 抗体结构的破坏;
● 隔离器集成
:在 OEB5 级隔离器内集成粒子监测(0.5 μm 和 5.0 μm 双通道)和浮游菌采样器(每 4 h 取样一次),数据实时传输至 MES 系统。
● 烟雾测试(Smoke Study)
:通过发烟装置模拟人员操作,确定干预动作的“安全区域”(如手臂活动范围≤ 30 cm);
● 爆瓶处理
:使用 5% 过氧乙酸灭活简单灭活后,用无尘布覆盖或包裹,待生产结束后清洁和消毒处理;
● 数据追溯
:每条灌装线配备电子批记录(EBR),记录干预次数、剔废数量等关键参数,以支持偏差调查。
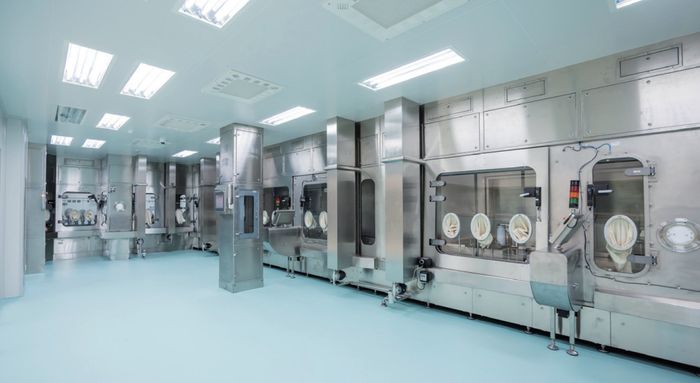
图3 隔离器
● 压差梯度控制
:隔离器内部维持合适的压差梯度,如理瓶段 35 Pa、灌装段 25 Pa、轧盖段 15 Pa。配备差压传感器,波动超 ±5 Pa 触发报警;
● VHP 生物净化
:先进行 PD 开发(VHP 生物净化程序开发),使用最少过氧化氢用量或最短维持时间达到生物净化效果,再延长维持时间进行PV。过程中使用生物指示剂 BI(嗜热脂肪芽孢杆菌)进行挑战试验,确保Log6 减少达标;
● 手套完整性测试
:每次使用前后对手套进行“压力衰减测试”,充气压力大于 500 Pa,维持一定时间后通过压力降确认手套的完整性;
● 隔离器内抽真空设计
:尽量避免使用抽真空设计,如无法避免,则在抽真空处加装 BIBO 过滤器,避免高活物质随抽真空动作扩散。
● 高活物质残留
:生产结束后,隔离器开门前需对隔离器内部进行喷淋冲洗,再用压缩空气吹扫。回风管路每周执行 WIP(在位清洗),使用注射用水喷淋清洗,消除 ADC 毒性小分子吸附;
● 人员培训
:操作人员需通过虚拟现实(VR)模拟考核,确保动作标准化,减少手套磨损导致的泄漏风险。
● 双真空计
:配备电容式和电阻式双真空计,能有效根据二者数据判断冻干过程中一次干燥的终点;
● 双级过滤器
:通气过滤器采用双级除菌过滤器,灭菌后在线进行完整性测试,确保生产过程中通入气体的无菌性;
● 生产前准备
:生产前需要进行冻干箱体在线清洗和在线灭菌,以及冻干机箱体泄漏率测试。
3.5 轧盖机与外洗机:终端密封与清洁保障(参见图4)
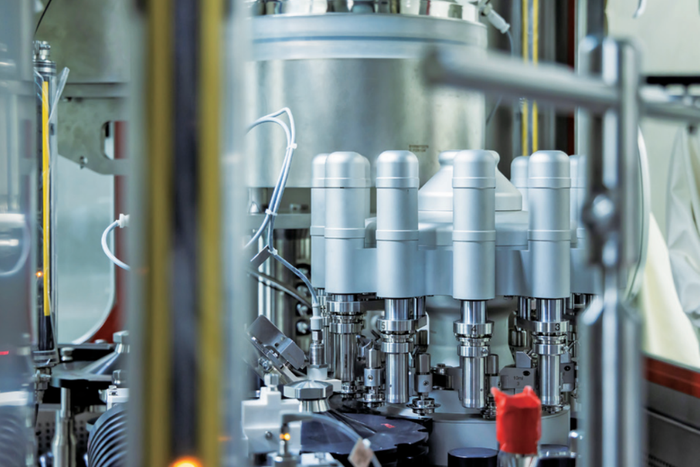
图4 轧盖机
● 压力反馈系统
:通过传感器实时监测轧盖压力(目标值:0.2~0.5 MPa),超限时报警;
● 铝屑控制
:在轧刀下方安装负压抽吸装置(风速≥ 0.5 m/s),铝屑收集效率> 99% ;
● 在线视觉检测
:采用 AI 图像识别技术,自动判断压塞高度,误判率< 0.1%。
● 清洗效果
:采用核黄素确认清洗覆盖率,再用淋洗水或擦拭取样检测清洗后残留;
● 灭活系统
:破瓶废水导入灭活罐,通过次氯酸钠等灭活剂灭活,满足 EPA 排放标准;
● 防微生物滋生
:水箱采用 316L 不锈钢材质,内壁电解抛光(Ra ≤ 0.4 μm),配备压缩空气吹扫功能,减少生物膜形成。
东曜药业苏州基地采用“一地化生产”模式,将抗体生产、ADC 偶联及制剂灌装集中布局,有效减少跨厂区运输导致的污染风险。其核心设施包括:
● 独立偶联车间
:3个车间物理隔离,其中 2 个用于高活 ADC、XDC 生产,1 个用于无毒偶联药物生产;
● 模块化设计
:灌装线可在 24 h 内完成规格切换(2R 至 50R 西林瓶),避免交叉污染。
● 数字孪生技术
:通过 3D 建模实时模拟设备运行状态,提前预测过滤器堵塞、压差异常等潜在风险;
● 大数据分析
:整合五年生产数据,建立“污染风险预警模型”,预警准确率高达 98%。
● GMP++ 体系
:在传统 GMP 基础上,增加“数据完整性审计”与“持续工艺验证(CPV)”;
● XDC 平台
:采用酶催化偶联技术,替代传统化学偶联,降低毒性小分子暴露风险。
●
高活药物的多元化:PROTAC、核素偶联药物等新型分子对 CCS 提出更高要求;
● 全球化供应链风险
:进口设备配件短缺可能影响维护周期。
● 连续制造(CM)
:通过封闭式连续灌装减少批次间清洁需求;
● 单抗传感器
:开发特异性生物传感器,实时检测残留毒性分子;
● 机器人协作
:采用 AGV+ 机械臂完成物料转运,实现“无人化无菌室”。
无菌制剂生产的交叉污染控制是一项系统性工程,需融合先进设备设计、智能化监控与严格的操作规范。东曜药业的实践表明,通过技术创新(如 XDC 平台、数字孪生)与精益管理(一地化生产、GMP++),可显著提升 CCS 的有效性与经济性。未来,随着生物制药的复杂度升级,交叉污染控制将从“被动防御”转向“主动预测”,为行业可持续发展提供坚实保障。
评论 0
没有更多评论了