SCADA:数据采集与监控系统的广域应用
SCADA系统,即数据采集与监控系统,是工业控制的核心。它集成了数据采集、数据传输和人机界面(HMI)软件,为操作员提供了一个集中监视和控制的平台。SCADA系统的设计初衷是为了收集现场信息,将这些信息传输到计算机系统,并以图像或文本的形式显示出来。这样,操作员可以从集中的位置实时地监视和控制整个系统,自动执行相关操作或任务。
SCADA系统的主要应用领域包括水处理、石油天然气管道、电力传输和分配系统、铁路等分布式系统。这些系统通常需要跨越广阔的地理区域,SCADA系统提供了一个有效的解决方案,以实现远程监控和控制。
DCS:分布式控制系统的过程控制
DCS,即分布式控制系统,主要用于同一地理位置环境下控制生产过程的系统。DCS系统通过集中监控的方式协调本地控制器执行整个生产过程,减少了单个故障对整个系统的影响。这种系统在炼油、污水处理厂、发电厂、化工厂和制药厂等工控领域中非常常见。
DCS系统与企业系统之间通常设置有接口,以便将生产过程体现在业务整体运作中。这种集成性使得DCS系统在现代化工厂中尤为重要,它不仅提高了生产效率,还增强了生产的灵活性和可扩展性。
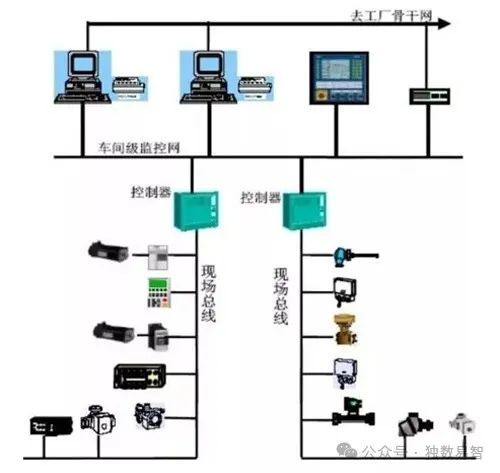
PLC:可编程逻辑控制器的现场控制
PLC,即可编程逻辑控制器,是在传统的顺序控制器的基础上引入了微电子技术、计算机技术、自动控制技术和通讯技术而形成的新型工业控制装置。PLC的目的是取代继电器、执行逻辑、记时、计数等顺序控制功能,建立柔性的程控系统。
在工业自动化和控制系统的网络体系结构中,PLC作为重要的控制部件,通常应用在SCADA和DCS系统中,用于实现工业设备的具体操作与工艺控制。PLC具有用户可编程存储器用于保存实现特定功能的指令,如I/O控制、逻辑、定时、计数、PID控制、通信、算术、数据和文件处理等。
三者的区别与联系
SCADA、DCS和PLC三者在工业控制系统中各有其特点和应用场景。SCADA和DCS更多地被视为系统概念,而PLC则是一种具体的产品。DCS主要用于过程自动化,PLC主要用于工厂自动化(生产线),SCADA则针对广域的需求。
从计算机和网络的角度来看,它们是统一的,区别主要在于应用的需求。SCADA可以被视为调度管理层,DCS是厂站管理层,而PLC则是现场设备层。这些系统在实现工业自动化的过程中,相互协作,共同确保了工业生产的高效和安全。
SCADA是调度管理层,DCS是厂站管理层,PLC是现场设备层
DCS是一种“分散式控制系统”,PLC(可编程控制器)只是一种控制“装置”,两者是“系统”与“装置”的区别。系统可以实现任何装置的功能与协调,PLC装置只实现本单元所具备的功能
随着技术的发展,SCADA、DCS和PLC之间的界限越来越模糊,它们之间的集成和协同工作变得越来越重要。了解这些系统的区别和联系,对于设计和实施有效的工业自动化解决方案至关重要。随着工业4.0的推进,这些系统将继续演进,以满足日益增长的工业自动化需求。
评论 0
正在获取数据......