文/ 赵瑞 范宇
笔者认为报警管理首先应该是整个QMS(QualityManagement System) 体系流程中最高管理层级的一部分,如图1 所示。
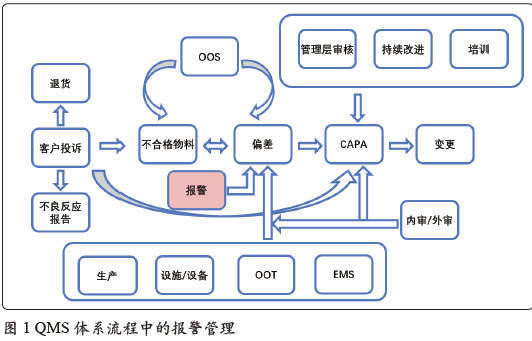
随着科技的发展,制药企业会在GMP 的六大系统中应用更多的自动化和信息化技术手段来提高管理和生产效率,这些自动化和信息化系统每天必然会产生大量的报警信息,基于GMP 管理的一般原则, 管理人员必须对这些异常事件作出响应和动作。但这一工作量是巨大的,不可能将这些工作汇集到QA 部门进行集中处理,因此必须对报警进行分类分级管理,并规定各级报警的应对措施,这样才能大大提升药品生产企业质量体系的管理效率。由于报警信息可能来自于各大体系,因此笔者建议将其作为企业的最高层级质量体系管理文件的一部分。 图2 展示了与GMP 六大管理体系相关的IT/OT系统。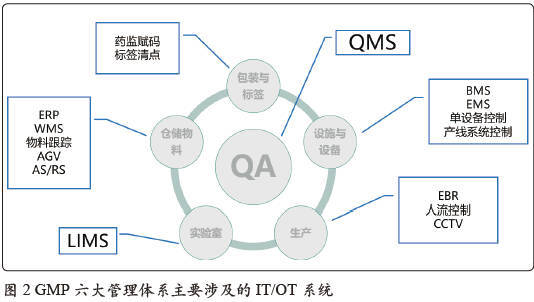
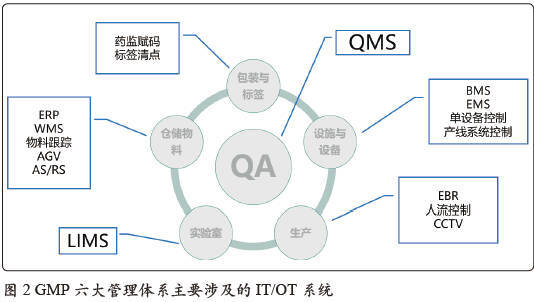
报警等级的分类借鉴GMP 中洁净室等级的分级方式,我们可以将报警等级分为四级,即A 级,B 级,C 级,D级。每一个级别的定义如下:
(1)“关键质量级别”报警(后续定义为A 级或者B 级)——报警发生时会对关键质量属性(CQAs)造成潜在影响。这种报警发生时需要人为干预以及评估,分析是否对CQAs 产生潜在影响。如果针对该报警管理事先有说明或者评估流程,该报警划分为B级。如果没有相关说明和评估流程,该报警划分为A 级。这些警报是否会产生偏差事件,取决于CQAs 评估的结果。
(2)“关键功能级别”报警(后续定义为C 级)——报警发生时对关键质量属性不会产生影响,但是会引起设备或者系统异常。这个报警有可能是直接完成或者在人为干预后完成。这个报警经验证可以完全消除对CQAs 造成的影响,并在重新生产前将设备恢复到已验证的工艺状态。
以日常运营的水系统为例,C 级报警在实际生产中的应用场景有:
• 纯化水机加药箱(次氯酸钠、亚硫酸氢钠、NaOH 等)低液位报警,报警提示不影响系统运行,人工补充药液后液位恢复正常,报警消除。
• 纯化水储罐液位低报警(补水异常),供水恢复后报警自动离开,无需人工干预。
• 超滤膜压差高报警、自动启动反洗程序,反洗结束后压差恢复正常,报警自动离开,无需人工干预。
(3)“非关键级别”报警(后续定义为D 级)——报警发生时对关键质量属性不会产生影响。该级别报警或消息可以帮助操作员更好地操控设备。
报警等级的决策
报警发生时,应该有一套非常严谨的决策系统帮助管理人员对报警信息进行分类,这个报警等级判定分类工作应该在系统上线前就已经做好(目前大部分企业做不到这一点),这样的决策过程需要系统供应商和生产企业管理人员共同参与。图3 展示了决策的整个过程。
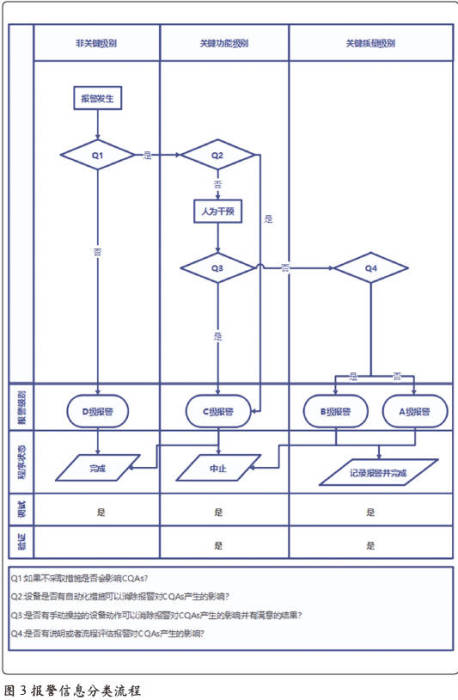
报警信息的处理
各级报警产生后,我们要针对不同级别的报警做出相对应的措施,不同的报警可以根据表1中的要求对设备和文件做出不同的规定。
上文的论述一般情况下针对以批为生产单位的工艺系统,在药品生产企业还有一种24×7 运行的系统,比如在线尘埃粒子监测,水系统水质在线监测等。针对这类系统,目前最常见的报警分类为警戒线报警& 行动线报警,并适用于以下原则:
• 警戒线报警用于商业监测/趋势分析,但并不影响CQAs(定义为D 级报警)。
• 行动线报警,这类报警可能会影响CQAs,定义为A、B 或者C 级。
• 对于警戒线报警,需要有长期存储的功能(存储数值/ 数据)用于趋势分析。
• 如果警戒线报警重复发生(在一定时间内连续发生警戒线报警),即便是定义为D 级,也可能会对CQAs 造成潜在影响。这种情况下,应触发特殊的行动线报警(定义为A、B 或者C 级;例如,粒子含量连续6 次警戒线报警),并按照行动线报警,进行相对应的调查以及分析。
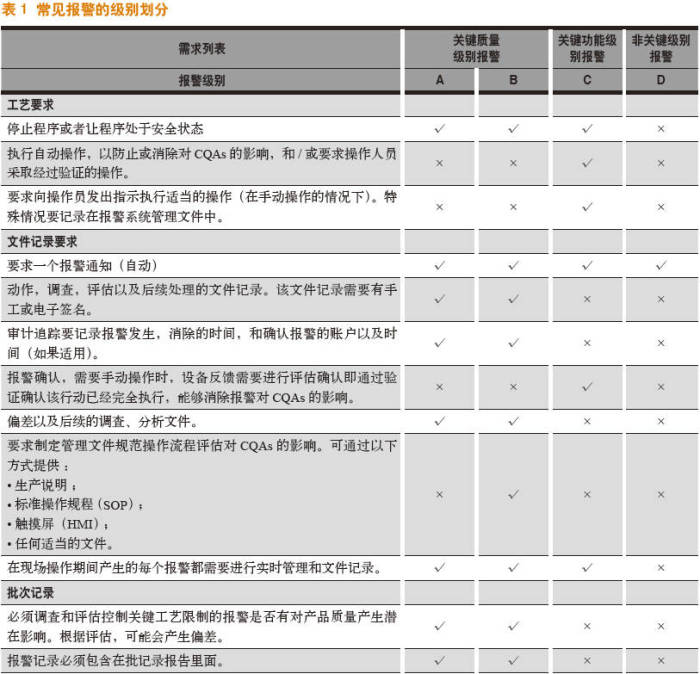
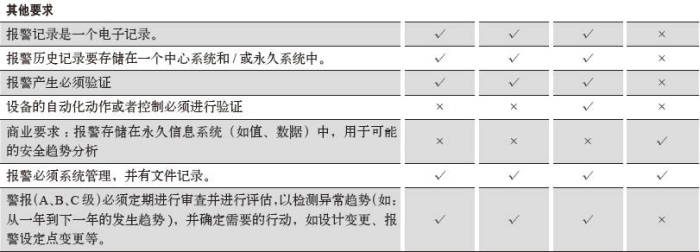
评论 0
正在获取数据......