为小批量生产量身定制的包装方案
Anke Geipel-Kern
2023-01-04
由于市面上没有合适的产品,Boehringer Ingelheim 公司自主研发了一种用于小批量生产的包装方案,进行小批量生产时,包装设备的准备时间和清洗时间远远超过生产所需的时间,Boehringer Ingelheim 公司的负责人认为从长远来看这样太不经济,于是便着手开发了 Future Pack,该产品将全新的设计与深思熟虑的生产工艺相结合,目前已经投入使用。
用2 min来烹饪,用 2 h 来打扫厨房卫生,任何一个专业厨师都会质疑这样的用时分配,然而这在药品包装生产过程中却司空见惯,完成生产只需 5 min,但让机器针对下一个生产订单做好准备工作则需耗时 2 h,现在许多制药企业都为此大伤脑筋,这是由小批量和非常小批量的药品包装生产趋势带来的问题。
有些抗肿瘤制剂的生产批量甚至为1,Boehringer Ingelheim公司的 Ingelheim工厂也面临相同的情况,“药店和诊所已经不再在仓库中装满抗肿瘤药物,而是按需订购,重要的是满足客户要求,关键词是以患者为中心。”Boehringer Ingelheim 的工艺工程师(自主开发 Future Pack 的项目经理)JanikJack 说道。按需生产意味着:员工需要将 20~30 个泡罩手工分拣至包装中,然后配上说明并准备发货,这不仅耗费时间,而且增加成本。
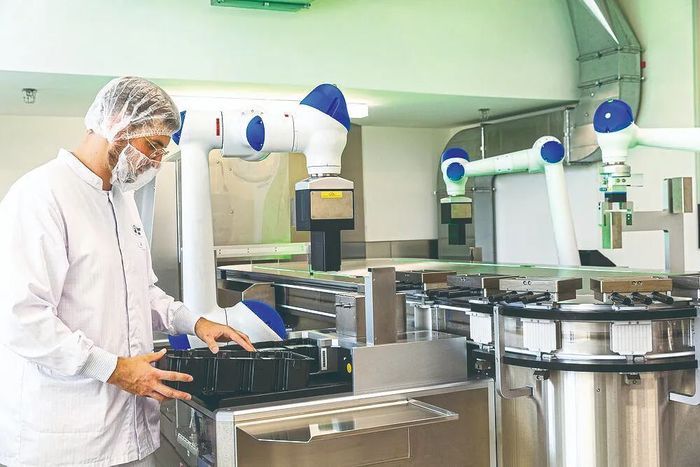
“传统包装设备对于大批量生产而言非常理想,但面对这些很小的批量时,完成生产订单实际上只需要几分钟,生产时间与准备和清洗时间完全不成比例。”Janik Jack 解释道。
设备制造商现在才开始应对这种挑战并开发相应的机器委实让人不解,但情况确实如此。“到目前为止,市场上还没有我们最适合小生产批量的包装机。”Janik Jack表示。于 是Boehringer Ingelheim开始自力更生,设立了一个名为“小订单包装”的项目,在完成该项目的过程中,人们不仅重新定义了包装工艺,而且还开发了一台设备,称之为 Future Pack。这台设备中的模块化设计、机器人技术、往返传输系统、泡罩定位、数字印刷系统等都是全新的,其中一部分是企业与相关供应商专门为 Future Pack 开发的。
在生产现场,设备的亮点清晰可见:一旦机器收到订单信息并通过手持扫描仪启动,模块就像被一只看不见的手控制一样开始工作。Future Pack 能够针对订单自行做好准备,接着对其进行加工处理并在生产结束后重新返回原始状态。
Janik Jack 领导的团队为此项目努力工作了 3 年,如今从 4 个模块天衣无缝的配合中已经完全看不出为了实现各种组件的编程和自动化,当时完成了多少工作和付出了多少努力。“开始时系统完全不合适,不是信号有误,就是信号太多或信号太少,去掉一个组件,机器就无法再启动”。今天 Janik Jack 可以笑谈这一切,但当时却不是这样,团队花了半年时间来应对所有的突发事件,才使得机器运转正常,每分钟加工8 个泡罩的非高速机器就此诞生。Janik Jack 说高速不是目的,机器的最大优势不在于速度,而是将高速系统从小订单中完全解放出来,另一个要点是:“针对每个商品订单,我们都从第一个泡罩开始生产,启动时间为启动时间为3~5 min,在此期间,清洗、准备工作完成,同时第一个泡罩也打印完毕。”Janik Jack 强调说。
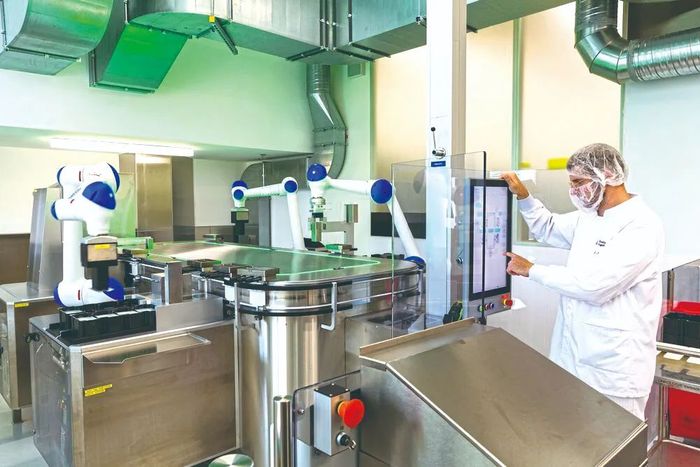
机器的中心是一条带有磁悬浮梭子的传输带,用于运输成型部件和泡罩。4 个模块各司其职地自动化运行:模块 1 负责成型部件的发送,两种泡罩规格中的每一种目前都有其自己的 6 个成型部件,它们存储在传输系统下方的掩体中。模块 2 负责泡罩发送,机械臂取出托盘上的泡罩并将其放在往返传输系统上,泡罩由此进入第三个打印模块,在那里以数字方式打印必要的药物信
息,打印文件是专门的 PDF 格式,
存放在经过验证的服务器上,系
统根据订单识别出需要的格式并
独立从服务器中提取正确的格式,
打印之后,相机会检查位置的正
确性、打印图像的质量和数据的易读性。生产过程快结束时,另
一个机器人模块移除打印好的泡
罩并将它们放回模块 4 提供的空托盘中,这时一名员工将其取出,最后手工完成最终包装和运输包装。
对于 Janik Jack 领导的团队来说,在技术术语中被称为后期定制的方案意味着需要对整个流程(从获得订单到最终包装)进行重新构思,最初所有药物订单都使用 Uhlmann 的 B 1240 完成泡罩包装和打印,包括相关工作,例如,
更换打印版、清空胶片、清洗以
及重新启动(这时空泡罩会产生
材料损失),如今这一切都已省略。
现在,这台机器执行其最擅长的工作:连续输送泡罩,每分钟可达 40 个,目前一次就能生产10 万个空白泡罩,然后每 40 个装
在一个托盘里,放在仓库中备用,
随后安装的 UV 打印机为泡罩提供二维数据矩阵代码,包括批号、材料号和精确到秒的时间戳。
Janik Jack 解释说,这样泡罩以后在仓库中可以清楚地归类。在机器人模块 1 中,UV 扫描仪会在抓取时检查每个泡罩,只有正确的材料才会被进一步加工处理,随后订单所需数量的泡罩在 Future Pack 中被印上订单特有的数据。
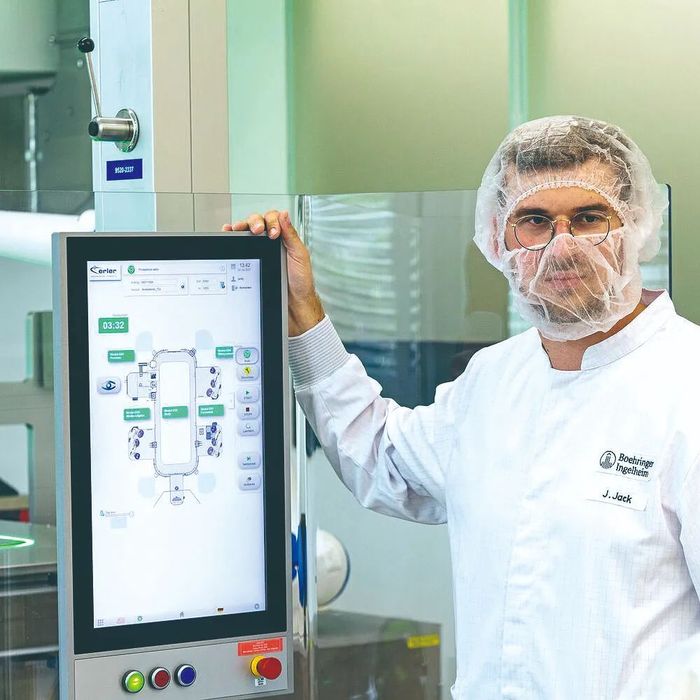
看似轻描淡写的纸上打印曾经也是一个挑战,在尝试解决它时,项目团队几乎绝望,而且还造成了巨大的延误。“在传统工艺中,薄膜来自卷筒并且表面光滑,而来自仓库的泡罩已经密封,这意味着薄膜经过温度和压力处理已经老化,在显微镜下显示出金字塔结构,即所谓的密封图像,使用传统墨水在上面打印,图像会不干净。”Janik Jack 解释道,墨水不能像在光滑的薄膜上那样正常流动,会出现斑点,如果增加墨水量,打印的图像又会因为流动而影响质量。“因此我们必须开发出一种新墨水,并由质量保证部门进行内部检查和批准。”这意味着连续几个月需要进行运行测试、稳定性检测以及等待墨水最终达到合适的粘度并通过所需的鉴定。
往返传输机上的泡罩定位也具有挑战性,为了确保装有泡罩的往返传输机到达打印头时总是处于相同的位置,开发人员设计了一种固定泡罩的真空机制,整
个过程由摄像头监控,以满足高
质量的标准。安全性绝对是一个特殊的主题:系统通过扫描仪、摄像头和传感器持续自行监控,一旦出现干预或错误,会立即被发现。RFID 读码器不断比较部件和往返传输机中内置的芯片,防止弄混,这使人为操控变得极其困难,测试时,Janik Jack 的团队费了很大力气才能骗过机器、设置错误。
如果员工想从外部进行干预,机器会关闭,之后保护屏障才会打开。实现机器人真正协助工作并在人类接近时减速运行的这一最初设想尚未实现,还有待进一步完善。
项目背后还隐藏着许多鲜为人知的工作:全新设计的生产流程自然也需要通过新的 SOP 来进行控制,相关部门需要新的文件,原来沿用的东西必须转换成 PDF文件等。重要的一项内容是数据矩阵代码,每项工作开始时机器都会被输入数据矩阵代码,该代码包含所有订单数据,从订单号开始,到批号、生产日期和有效期,再到需要打印多少个泡罩的信息。现在这些代码仍采用人工扫描,但从中期来看,人们计划将 Future Pack 与整个集团的 MES连接起来,目前还在进行实际测试,如果机器运行正常,订单规模的发展也符合预期,那么就会有更多的模块加入进来,使至今为止依然手工完成的最终包装实现自动化。
评论 0
正在获取数据......