如何打好退火工艺中温度和时间的组合拳?
在《冻干工艺设计:你退火了吗?》(https://mp.weixin.qq.com/s/Uvv9Tr1aDekxJy2E2Qt7rA)之后,退火工艺以及退火参数设置引起了同行们兴趣和关注。本文作为续集二,在续集一《你的退火温度是最优解吗?》之后,对冷冻干燥工艺中的退火参数设置进行深入探讨。欢迎各位同行参与交流讨论、批评指正、提出宝贵的观点和意见。
言归正传,在《冻干工艺设计:你退火了吗?》一文中提出:“退火温度越高,需要达到完全结晶需要的退火时间越短;退火温度越低,需要达到完全结晶需要的退火时间越长。”由此可见,退火温度与退火时间是一组组合拳,退火温度和退火时间均设定得当,才能得到理想的冻干参数。在《你的退火温度是最优解吗?》一文中对冻干工艺参数中的退火温度有详细的介绍,其中提到:“退火温度应该介于玻璃化转变温度和共熔温度之间”。那么,冻干工艺参数中的退火时间有没有最优解?退火时间是不是越长越好?
如果说退火温度如同拳击中的不同级别,例如重量级、中量级、轻量级、羽量级;那么退火时间如同不同选手的持续战斗力。如果选择错了退火温度,就如同一个优秀的羽量级的选手参加一个重量级的比赛,虽然战斗力很强横也没有太多优势。退火温度选择得当,退火时间能起到四两拨千斤的效果,如果退火温度不当,会导致退火时间延长,浪费人工水电等资源,造成成本无谓增加。所以,退火时间不并不是越长越好。由此可见,在设定恰当的退火时间之前,要先设定恰当的退火温度。在恰当的退火温度下,摸索退火时间,才能起到事半功倍的效果。退火温度设定参看续集一《你的退火温度是最优解吗?》,本文将探讨如何设定退火时间。
李恒乐等考察在不同退火时间对冷冻干燥过程的影响。首先将物料S在-32℃的温度下冷冻成型,随后将温度升高至-10℃分别进行退火处理5h和10h,退火完成以后,将物料S温度再次降低到-32℃,保证物料S在实验开始前具有初始的冷冻温度。将经过-10℃分别进行退火处理5h和10h与未经过退火处理的物料S在相同的冻干参数下进行冻干,得到退火对物料S干燥过程的影响实验曲线。
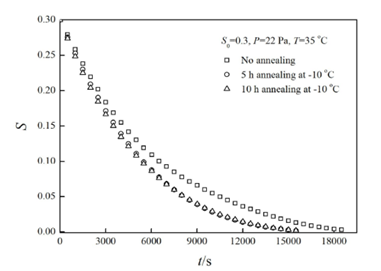
在温度35℃和压力22Pa干燥条件下,采用-10℃退火处理的物料S干燥效率高于未经退火处理的物料S。而采用-10℃退火处理5h和10h的物料S干燥效率无显著差异。
经-32℃预冻后,物料S大部分形成结晶,仍存在小部分物料S未完全结晶。在干燥过程中,小部分未完全小冰晶受热面积与大冰晶相比更大,所以小冰晶升华更快,留下错综复杂的升华孔道,不利于水气逸出。大冰晶在升华时,水气要经过错综复杂的升华孔道。经过-10℃退火处理的物料S,通过奥式熟化,小部分未完全结晶的物料S有机会再次结晶,形成大冰晶,在干燥过程中,大冰晶升华时,留下疏松的升华孔道,更加有利于水气进一步升华。
而采用-10℃退火处理5h和10h的物料S干燥效率无显著差异,说明-10℃退火处理5h,通过奥式熟化,小部分未完全结晶的物料S已经充分再次结晶,形成大冰晶,充分完成奥式熟化过程。继续延长-10℃退火处理时间,对冰晶的改善无显著影响。考虑到时间成本和资源的节约,所以优选-10℃退火处理5h。
陈景生等考察在不同退火时间对注射用氨磷汀冷冻干燥过程的影响。采用-30℃对氨磷汀溶液进行预冻,分别采用未退火工艺和不同退火时间3h、6h的工艺制备样品。根据样品的批间水分含量的相对标准差作为评价指标,并对不同样品进行XRD表征,不同样品XRD衍射图如下。
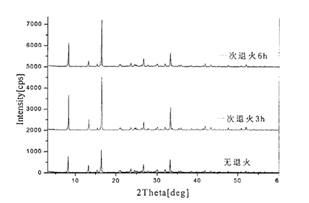
Figure2:注射用氨磷汀不同制备工艺的XRD衍射图谱
采用退火工艺制备的样品,批间水分含量的相对标准差平均小于6%;未采用退火工艺制备的样品,批间水分含量的相对标准差平均小于11%。而不同退火时间3h、6h的工艺制备样品,批间水分含量的相对标准差平均小于6%。未采用退火工艺制备的样品与采用退火工艺制备的样品XRD衍射图谱存在较大差异,而不同退火时间3h、6h的工艺制备样品XRD衍射图谱无显著差异。
由此说明采用退火工艺,可以使样品预冻后形成的部分小结晶重塑成大结晶,拥有大结晶的样品在冷冻干燥过程中制得的样品水分含量更均一。因为通过退火工艺,样品的结晶发生改变,增加了注射用氨磷汀晶体结晶强度,导致XRD衍射图谱发生改变。
而不同退火时间3h、6h的工艺制备样品,批间水分含量的相对标准差平均小于6%说明,通过退火3h,小部分未完全结晶的物料已经充分再次结晶,充分完成奥式熟化。继续延长退火时间对奥式熟化无进一步帮助。退火时间6h的工艺制备样品与3h的工艺制备样品的XRD衍射图谱无显著差异说明,退火3h的工艺制备样品增加注射用氨磷汀晶体结晶强度与退火6h相当。
夏鹏等考察退火时间与退火温度的影响。采用10%的蔗糖溶液,将溶液灌装后半加塞,-60℃预冻,采用-40℃、-30℃、-20℃、-10℃、-5℃、-3℃六组退火温度和0.5h、1h、2h、3h、4h、5h六组退火时间共36组实验,以一次干燥平均速率为评价指标。实验结果如下:
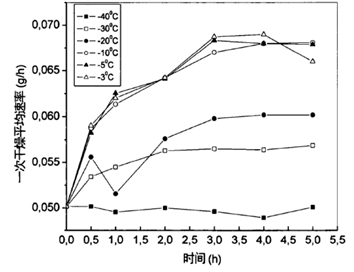
Figure3:不同退火温度和退火时间对一次干燥平均速率的影响
根据实验结果可知,退火温度为-40℃时,该温度低于玻璃化转变温度,样品的结晶没有发生变化,所以干燥速率随着退火时间延长无明显变化。
从-30℃到-10℃,随着退火温度升高,一次干燥平均速率升高。在特定的退火温度下,如-30℃退火,随着退火时间延长,一次干燥平均速率先升高,然后趋近平稳。说明随着退火时间延长,奥式熟化逐渐完成。充分奥式熟化后,样品的结晶不再发生明显变化,所以一次干燥平均速率先升高,然后趋近平稳。
从-10℃到-3℃,随着退火温度进一步升高,一次干燥平均速率没有进一步升高,说明退火温度已经趋近于晶体融化温度,如果进一步提高退火温度,会导致晶体融化,不利于后续干燥。
退火温度越高,增加相同退火时间,提升的一次干燥平均速率越多。退火温度越高,增加退火时间的空间越大,例如在-30℃退火,退火2h后,再增加退火时间,对一次干燥平均速率无进一步提升;而在-10℃退火,退火3h后,增加退火时间,对一次干燥平均速率仍然有提升效果。
总结上述三个案例,说明退火温度和退火时间是一组组合拳。案例一和案例二筛选的退火时间都可以满足需求,而且退火时间有进一步优化的可能性。结合案例三可知选定恰当的退火温度,在该退火温度下,筛选恰当的退火时间,才能把冷冻干燥速率提升到最佳状态。理论上,退火时间越长,小结晶奥式熟化越充分,形成的结晶越完美。然而,在一致性评价和集采的大背景下,结合药厂的生产实际情况,控制成本的需要愈发迫切,在保证产品质量的同时,要兼顾生产的成本。冷冻干燥的曲线优化是不可回避的问题,在权衡冻干成本和产品质量的时候,要保证产品质量,退火时间不能过短,要兼顾冻干成本,退火时间又不能太长,于是退火时间有了最优解。
1.李恒乐,具有预制孔隙多孔物料冷冻干燥实验.2017
2.陈景生,两种水溶性冻干制剂的制备工艺优化研究.2009
3.夏鹏,药品冷冻干燥装置的优化及实验研究.2005
来源:药事纵横
评论 0
正在获取数据......