注射用水是药品生产的重要原料之一,其质量直接影响到药品的有效性和安全性。根据药典规定,注射用水必须符合微生物限度、无菌性、内毒素限度等质量标准。这就要求注射用水生产过程中必须采取有效的消毒措施,杜绝微生物污染,以保证注射用水质量符合要求。在注射用水生产系统中,储配系统往往也是微生物污染的重灾区。储配系统一旦发生污染,可能导致大量污染注射用水进入药品生产,严重危害药品质量和用药者的健康。开发高效的储配系统消毒技术,对保证注射用水质量来说意义重大。
注射用水储配系统由注射水制备系统、储水罐、输配管道、消毒系统、输配泵等部件组成。目前大多数制药企业的注射用水储配系统结构设计存在回流管路过于复杂、储水罐内部空间过大、使用点过多等问题。统计数据显示,我国约80% 的注射用水储配系统管道总长超过 300 米,平均使用点数达到 50 个以上,管道回路数量可达 15 条。过于复杂的回流管道会形成大量死角,管道长度过长增加了微生物滋生的机会。
注射用水储配系统的技术方案直接影响系统的微生物控制效果。目前一些常见的技术方案存在如下问题。
(1)循环消毒间隔时间过长间隔时间每延长 1 小时,注射用水微生物指标超标的概率就提高 17%。间隔时间过长将导致储配系统在非消毒期间累积大量微生物。
(2)消毒温度不足热力学研究表明,微生物的死亡率与温度呈指数关系。当温度每升高 1℃,细菌的死亡率提高1 倍 ; 每个 10℃的升高,细菌死亡率提高 1000 倍。一些技术方案的消毒温度只有 90℃左右,远不能达到完全灭菌的效果。
注射用水储配系统所用管道及阀门等材料的选择对系统的微生物污染也会产生影响。统计数据显示,PVC 管道在121℃高温灭菌条件下,每升管道会释放出 2mg 的阻燃剂,这些化学物质混入注射用水中将增加患者肝肾负担。金属管道和阀门长期与注射用水接触也会产生铁锈等化合物。特氟龙阀门在高温情况下会释放出微量氟离子。根据药典规定,注射用水中氟离子的限量为 0.2ppm。而一些低质量的特氟龙阀门在灭菌过程中可释放出 0.5ppm 的氟离子,明显超出标准限量。
纯蒸汽灭菌是一种成熟的注射用水储配系统灭菌技术方案。该方案采用 121℃、压力 2.5bar 的纯蒸汽进行灭菌,灭菌时间为 30 分钟。在灭菌开始前,要先将注射用水储罐内的水完全排空,保证储罐内部处于干燥状态。然后由纯蒸汽发生器产生纯蒸汽,纯蒸汽发生器采用蒸汽锅炉加热蒸馏水,经过净化处理生成纯度超过 99.9% 的纯净蒸汽。纯净蒸汽流量设计为每小时 500 公斤,温度稳定在 121℃ ±1℃。经过管路输送进入储罐进行灭菌,管路直径为 80mm,材质为 316L 不锈钢 [1]。
过热水灭菌是一种广泛应用于注射用水储配系统灭菌的技术方案。其采用 121℃ 高温和压力相结合的方式进行灭菌。具体操作时,首先打开排放阀门,使注射水储罐中的液位降至设定的 40% 左右。随后启动循环泵,流量设置为每小时 2 立方米,将储罐中的水送到使用点,再回流循环到储罐中 [2]。
①工艺对比过热水灭菌和纯蒸汽灭菌时温度都需要达到121℃,持续循环 30 分钟。不同点在于过热水消毒不需要加入新的介质,对注射水进行保压加热满足温度要求即可,而纯蒸汽消毒要先对系统内的注射水罐进行排空,再通入纯蒸汽满足温度要求才可完成灭菌 [3]。②灭菌时间对比纯蒸汽灭菌系统循环时通入注射水罐的蒸汽需保压加热至 121℃,考虑到纯蒸汽灭菌系统各使用点在升温过程中产生蒸汽冷凝水,由疏水器排出的过程产生热量损耗,从而增加灭菌时间。根据 GMP 要求,注射用水须达到 70℃以上的循环温度。对比可知,过热水灭菌系统采用消毒换热器和储罐夹套共同加热注射用水的方式,保压加热注射用水至 121℃所用时间明显低于纯蒸汽灭菌加热时间。③成本能耗对比纯蒸汽灭菌过程所需蒸汽量大,须单独设计一路纯蒸汽发生器提供灭菌所需蒸汽。灭菌系统中各使用点须安装疏水器和温度探头。使用点越多,耗材越多。对比可知,过热水灭菌只需在消毒换热器前后装备温度探头即可实现全程控温从而达到灭菌温度要求 [4]。④灭菌效率对比过热水灭菌过程中高温高压注射水充满储配管网以及各使用点,灭菌效率更高。尤其是经过各使用点(采用 U 型回弯设计)时,纯蒸汽灭菌相比较过热水灭菌容易产生灭菌死角。综上所述,过热水灭菌方式有利于系统复杂,使用点多的系统。其操作方式简单,运行成本低,用途更为广泛 [5]。
以兰州生物制品研究所疫苗项目楼中一条注射用水输配环路系统为例,对过热水灭菌过程分析如下。
当注射用水系统回水微生物限度达到警戒线或是纠偏线时,应对注射用水系统进行灭菌处理。注射用水系统每一年须进行一次灭菌,注射用水输配系统采用 125℃过热水灭菌处理。注射用水输配系统可能因停电、循环泵故障、循环管路中的阀门异常关闭等因素导致循环中断系统停滞时间超过3 小时,系统恢复正常后对循环系统进行灭菌操作。
①液位调整:开启排放,注射水罐液位自动调整至40%。消毒换热器的工业蒸汽进气阀和冷凝水排放阀自动打开。消毒换热器温度开始上升,温度上升至设定值 125℃。②灭菌:当消毒换热器温度达到 125℃时,开始计时 60 分钟。③冷却:当消毒换热器温度达到 125℃,计时满 60 分钟后,灭菌结束,开始进入冷却程序。冷冻水进回水阀自动打开,系统进入冷却程序,循环温度下降至 95℃,冷却结束。④排水:冷却结束后,系统开启排放阀,将注射用水储罐液位调整至 15%,灭菌结束。灭菌程序见图 1 所示。
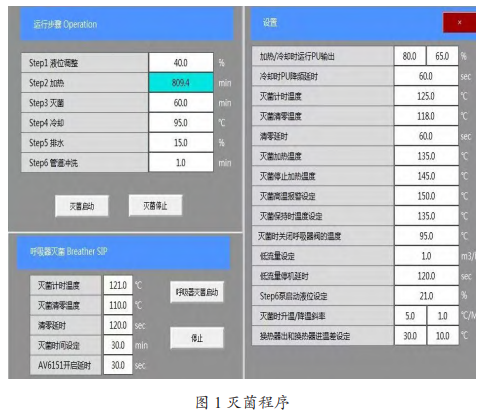
3.3 呼吸器作用
呼吸器是安装在注射用水储罐顶部的通气装置。由于注射水罐液位在生产时会不断变化,储罐内气体压力会不断变化,呼吸器的作用就是调节注射用水储罐中气体的进出使得压力平衡。呼吸器中的滤芯也会阻止外界颗粒和微生物进入注射用水储罐。为了杜绝一切污染源,通常注射用水循环系统灭菌时呼吸器也要进行灭菌。
3.4 呼吸器灭菌操作程序
当注射水储配环路灭菌结束后,再单独开启呼吸器灭菌程序。点击“呼吸器灭菌启动”,长按 3s。呼吸器灭菌程序开启。开启灭菌后,呼吸器进出气阀门自动关闭,纯蒸汽进气阀门开启,冷却水排放阀开启。开始升温,温度达到121℃时呼吸器灭菌开始计时,计时 30 分钟,纯蒸汽进水阀和冷却水排水阀关闭,呼吸器灭菌结束。灭菌程序见图 2。
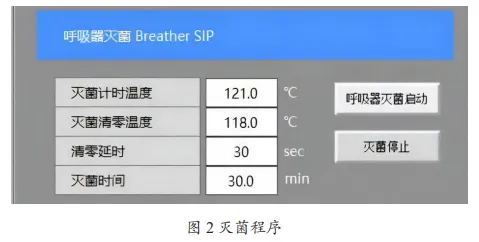
4 灭菌方案改进分析
4.1 原方案分析
对比此案例注射用水输配系统的灭菌程序分析可知,该注射水输配系统所采用的过热水灭菌方式分两部分完成。第一步是对该输配系统管网和注射用水储罐进行灭菌。第二步是对储罐顶端呼吸器进行单独灭菌。这样分两步灭菌的方式比较繁琐也大大增加了整个系统的灭菌时间,同时呼吸器采用纯蒸汽灭菌会产生能耗。
4.2 改进方案分析
对于注射水储罐呼吸器的灭菌一般有两种方案,见图 3。
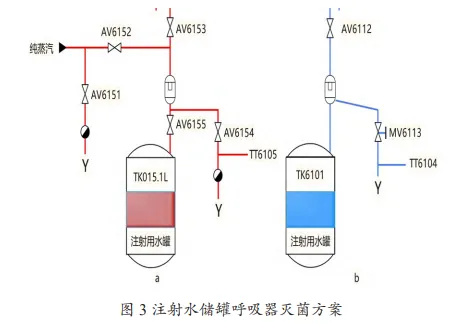
第一种是呼吸器与罐体通过阀门 AV6155 断开采用121℃蒸汽单独灭菌,见图 3a;第二种是呼吸器和注射用水储罐一同灭菌,如 121℃高温水灭菌或者 121℃蒸汽灭菌,见图 3b。
图 3a 所示是疫苗项目楼中一条注射用水输配环路呼吸器灭菌工艺图。此灭菌是正向灭菌,纯蒸汽在呼吸器滤芯上端注入,然后下端排出的灭菌工艺。灭菌程序开始时呼吸器上下端气动隔膜阀 AV6153 和 AV6155 关闭,气动隔膜阀AV6152 打开,纯蒸汽通过阀 AV6152 进入呼吸器进行灭菌。灭菌过程中气动隔膜阀 AV6151 和 AV6154 打开,用来排放灭菌时产生的蒸汽冷凝水。
图 3b 所示就是相对于目前疫苗项目楼中一条注射用水输配环路呼吸器灭菌工艺做出的改进方案工艺图,此灭菌是反向灭菌。当注射水输配环路灭菌开始计时时,储罐液位 40%,此时储罐温度达到 121℃并持续保温保压,注射水储罐上端会产生大量蒸汽,蒸汽由呼吸器下端进入呼吸器滤芯,灭菌时呼吸器上端气动隔膜阀 AV6112 关闭。灭菌产生的蒸汽冷凝水隔膜阀 MV6113 排出。
为了保证呼吸器灭菌时温度达到 121℃符合灭菌要求,呼吸器灭菌冷凝水排放时需要对温度进行实时监测,见图3 中 a、b 所示,温度探头 TT6105、TT6104 监测温度达到121℃持续 30 分钟即可完成呼吸器灭菌。
4.3 改进方案的优势分析
综合上述分析流程可知,选用注射用水储罐和呼吸器一同灭菌的方案存在显著优势,从时间上看呼吸器系统单独灭菌所用时间明显多于呼吸器随储罐一同灭菌所用时间。从成本能耗方面来看,呼吸器单独灭菌所用纯蒸汽需设单独管路供入,纯蒸汽进入呼吸器时损耗产生的冷凝水需设置疏水器排出。
5 结束语
随着先进技术的发展,现在的注射用水储配系统的灭菌技术已经变得十分便捷成熟。相信有更加完善便捷的高效灭菌方案须要发现并论证,当然,不管技术方案怎样改变,注射用水系统灭菌时符合标准的必要条件还是我们遵守的基础。
[1] 任金亮 . 制药用水储存及分配系统的消毒与灭菌 [J]. 流程工业 ,2015,(15):49-50.
[2] 冯庆 , 黄浩 . 制药用水储存及分配系统设计 [J]. 医药工程设计 ,2010,31(1):16-25.
[3] 关 一 鸣 . 谈 制 药 用 水 系 统 的 清 洁、 灭 菌 [J]. 科 技 创 新 与 应用 ,2012,(28):132
[4] 吕 峰 . 生 物 制 药 中 注 射 用 水 系 统 研 究 [J]. 化 工 设 计 通讯 ,2018,44(11):198-199.
[5] 朱 世 斌 . 解 读 新 版 GMP 对 制 药 用 水 系 统 的 要 求 [J]. 机 电 信息 ,2012,(23):1-9.
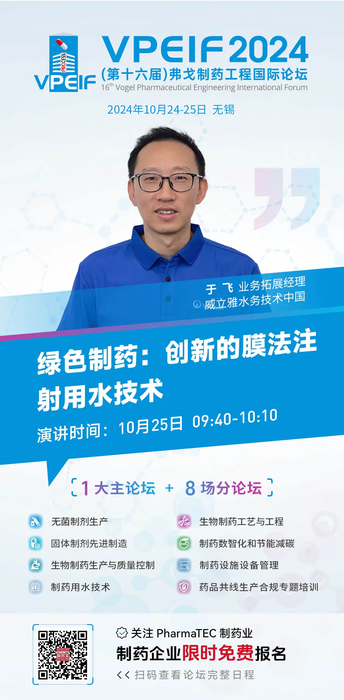
张会民、丁瑞辰、唐兴隆、曹帅 兰州生物制品研究所有限责任公司
邵丽竹
何发
评论 0
没有更多评论了